Now IS THe Time To...

Crawl Space Services In Knoxville, TN
Stetson Howard: 865-432-6743
CRAWL SPACE ENCAPSULATION, REPAIR, WATERPROOFING & MOLD REMOVAL
No-Obligation, Free Inspections
No-Obligation Free Estimates
We Warranty All of Our Work
100% Satisfaction Guaranteed
When it comes to protecting your home or commercial building from water damage, selecting the right waterproofing material is essential. From EPDM rubber and PVC membranes to liquid-applied coatings and bituminous membranes, there is a wide range of waterproofing options available, each designed for specific surfaces, environments, and conditions. With so many choices, it can be overwhelming to decide which material is best suited to your project’s unique requirements.
This guide will walk you through the most common waterproofing materials, outlining their key benefits and best-use cases, helping you make an informed decision to ensure long-lasting protection for your property.
Factors to Consider Before Choosing Waterproofing Materials for Your Foundation
Selecting the right waterproofing material for your foundation is a crucial decision that will affect the long-term durability and protection of your home or building. There are several key factors to consider, ranging from the type of foundation to the local soil and climate conditions. By understanding these factors, you can choose a waterproofing solution that meets your specific needs and ensures lasting protection against moisture infiltration.
Type of Foundation
The type of foundation plays a critical role in determining which waterproofing material is most appropriate. Each foundation type has different vulnerabilities and structural characteristics that impact how waterproofing solutions should be applied.
- Concrete Foundations: These are solid and relatively resistant to water, but cracks can still develop over time. Waterproofing materials like liquid-applied membranes or rubberized coatings are ideal for sealing potential cracks and providing a continuous barrier.
- Block Foundations: Block foundations are more porous than poured concrete and can allow water to seep through the joints. Sheet membranes or external coatings are often recommended to fully seal the foundation and prevent water infiltration.
- Poured Concrete vs. Masonry: Poured concrete tends to have fewer joints and gaps, making it more resistant to water penetration compared to masonry. However, masonry foundations require extra attention to joints, and waterproofing solutions such as elastomeric coatings or waterproof cement are often used to seal them.
- Crawl Space vs. Basement Foundations: Basements typically require more robust waterproofing solutions due to higher exposure to groundwater and hydrostatic pressure. Crawl spaces, on the other hand, may need vapor barriers and proper drainage systems to prevent moisture buildup.
Soil Conditions and Drainage
Soil type and drainage patterns around your foundation are significant factors that influence the selection of waterproofing materials. Different soils interact with water in various ways, affecting the pressure and moisture that your foundation is exposed to.
- Clay Soil: Clay retains water and increases hydrostatic pressure against the foundation, which can cause cracks and water infiltration. For foundations in clay soil, you’ll need waterproofing materials that can handle constant moisture and pressure, such as thick sheet membranes or external coatings.
- Sandy Soil: Sandy soil drains well, which reduces the amount of water against your foundation. However, sandy soil can shift and move, requiring flexible waterproofing solutions like liquid-applied membranes that can adapt to these shifts without cracking.
- Poor Natural Drainage: In areas with poor natural drainage, water tends to pool around the foundation, increasing the risk of seepage. In such cases, additional protection like drainage systems and highly resistant waterproofing membranes may be necessary to keep water away from the foundation.
Water Table and Climate
The local water table and climate are key considerations when choosing a waterproofing material for your foundation. Areas with high water tables or frequent rain require stronger, more moisture-resistant materials, while cold climates demand protection from freeze-thaw cycles.
- High Water Table Areas: If your property is located in an area with a high water table, your foundation will be under constant pressure from groundwater. This requires a robust waterproofing system, such as multi-layered membranes or bentonite clay sheets, which expand to seal cracks when exposed to water.
- Wet or Humid Climates: In consistently wet or humid climates, waterproofing materials with high moisture resistance are crucial. Liquid-applied waterproofing membranes or rubberized coatings that create a seamless barrier are excellent choices for these environments.
- Cold Climates and Freeze-Thaw Cycles: In colder climates, where water can freeze and expand within foundation cracks, materials that are flexible and resistant to freeze-thaw cycles are essential. EPDM rubber membranes or elastomeric coatings are recommended because they remain flexible and durable in low temperatures.
Budget and Longevity
While cost is an important factor, it’s essential to balance your budget with the long-term performance and durability of the waterproofing material you choose. Some materials may have lower upfront costs but require frequent maintenance or reapplication, while others offer long-lasting protection with minimal upkeep.
- Short-Term Budget Constraints vs. Long-Term Maintenance Costs: If you’re working with a limited budget, there are affordable options like liquid-applied membranes that can be effective in the short term. However, these may require more frequent reapplication compared to higher-end options like sheet membranes or bentonite systems.
- Durability of Materials and Reapplication: Consider the durability and lifespan of the materials you’re choosing. More durable waterproofing systems, like multi-layered membranes or rubberized coatings, may have a higher initial cost but will last much longer and require less maintenance over time.
- Balancing Cost with Performance: It’s important to find a balance between your budget and the effectiveness of the material. Investing in high-quality waterproofing solutions up front may save you from costly repairs or water damage in the future, making it a worthwhile long-term investment.
By carefully considering the type of foundation, soil conditions, water table, climate, and your budget, you can select the most effective waterproofing material for your foundation. Choosing the right solution will protect your foundation from water damage, extend its lifespan, and reduce the need for costly repairs over time.
Common Types of Foundation Waterproofing Materials
When it comes to protecting your foundation from water damage, selecting the right waterproofing material is essential. Each type of waterproofing solution offers unique features, benefits, and drawbacks, making it important to choose the one that best suits your foundation type and environmental conditions. Below is an overview of the most commonly used materials for foundation waterproofing and their characteristics.
Liquid-Applied Membranes
Liquid-applied membranes are a popular waterproofing option due to their flexibility and ease of application, particularly for irregularly shaped foundations or areas with difficult access.
How it works: These waterproofing coatings are applied directly to the foundation surface in liquid form. Once cured, they form a seamless, rubber-like membrane that provides a flexible and watertight barrier.
Best for: Foundations with irregular shapes or hard-to-reach areas, such as around corners, pipes, and tight spaces where sheet-based materials may be difficult to apply.
Pros:
- Seamless application means no joints or seams that could lead to leaks.
- Flexible, allowing the membrane to conform to various surfaces and bridge minor cracks.
- Easy to apply around corners and edges, making it ideal for complex foundations.
Cons:
- Surface preparation is critical; a poorly prepared surface can lead to adhesion problems.
- Typically requires multiple coats to achieve the desired thickness.
- Vulnerable to damage during installation, requiring careful handling to avoid punctures or tears.
Sheet-Based Membranes
Sheet-based membranes are pre-formed waterproofing sheets that offer consistent thickness and reliable protection, especially for larger, flat foundation surfaces.
How it works: These pre-formed sheets are applied over the foundation walls and sealed at the joints. The sheets are adhered using mechanical fasteners or adhesives and must be carefully sealed to prevent water from penetrating through the seams.
Best for: Large, flat surfaces that require uniform coverage, such as poured concrete foundations in commercial or residential buildings.
Pros:
- Provides uniform thickness, ensuring consistent protection across the entire surface.
- Durable and highly effective against groundwater, making it ideal for areas with high water pressure.
- Offers reliable long-term performance when properly installed.
Cons:
- Requires professional installation to ensure proper adhesion and joint sealing.
- Improperly sealed joints can lead to water leakage, reducing its effectiveness.
Bentonite Waterproofing
Bentonite clay membranes are known for their self-sealing properties, making them a unique and eco-friendly solution for foundation waterproofing.
- How it works: Bentonite clay naturally swells when exposed to moisture, expanding to fill gaps, cracks, and joints in the foundation. This swelling action creates a watertight barrier that helps prevent water infiltration.
- Best for: Below-grade foundations, especially in areas with high water tables or where groundwater pressure is a concern.
Pros:
- Self-sealing properties make it effective in sealing minor cracks or gaps in the foundation.
- Eco-friendly and made from natural materials, making it a sustainable option.
- Performs well in a variety of climates, particularly in wet conditions.
Cons:
- Limited flexibility in very dry environments, as it relies on moisture to function.
- May require additional layers or reinforcement in some areas to ensure full effectiveness.
Cementitious Waterproofing
Cementitious waterproofing is a commonly used, cost-effective solution for indoor applications, such as basements and crawl spaces.
How it works: Cementitious waterproofing involves mixing cement-based materials into a slurry and applying it to the foundation surface. Once cured, it forms a rigid barrier that blocks water infiltration.
Best for: Interior foundation waterproofing, especially in basements, crawl spaces, and other areas where moisture protection is needed but flexibility is less critical.
Pros:
- Easy to apply with standard tools like brushes or trowels.
- Cost-effective, especially for smaller residential projects.
- Ideal for concrete foundations and can be applied to both interior and exterior surfaces.
Cons:
- Not flexible, making it prone to cracking over time, particularly in areas with ground movement or temperature fluctuations.
- Requires a smooth, stable surface for optimal adhesion and performance.
Elastomeric Coatings
Elastomeric coatings are flexible, rubber-like coatings that offer excellent waterproofing protection, especially in areas exposed to high moisture or fluctuating temperatures.
How it works: Applied in liquid form, elastomeric coatings cure into a highly flexible, durable membrane that can stretch and contract with the movement of the foundation without losing its integrity.
Best for: Foundations in areas with high moisture exposure, such as wet climates, or regions with extreme temperature changes where flexibility is important.
Pros:
- Highly durable and resistant to both water and temperature extremes.
- Flexible enough to bridge small cracks, making it ideal for areas with foundation movement.
- Long-lasting, offering robust protection for many years with minimal maintenance.
Cons:
- Can be more expensive than other waterproofing options.
- Professional application is often recommended to ensure proper coverage and durability.
Each of these waterproofing materials offers unique benefits and is best suited for specific foundation types and environmental conditions. By considering your foundation’s needs, local climate, and long-term maintenance goals, you can select the right material to protect your home or building from water damage.
How to Choose the Right Waterproofing Material for Your Foundation
Selecting the best waterproofing material for your foundation is a critical decision that ensures long-term protection from moisture and water damage. To make the right choice, it’s important to evaluate the foundation’s condition, understand water exposure risks, consider installation requirements, and assess the longevity and warranties of different products. Below is a step-by-step guide to help you choose the best waterproofing material for your foundation.
Assess the Condition of Your Foundation
Before choosing a waterproofing material, it’s essential to evaluate the current condition of your foundation. This will help you determine whether the foundation needs repair before
waterproofing or if it’s ready for immediate application.
- Check for Cracks, Leaks, or Signs of Water Damage: Inspect your foundation for any visible cracks, leaks, or damp areas. If you find water damage, you’ll need to repair these issues before applying any waterproofing material. Small cracks may be sealed with flexible membranes, while larger structural issues may require more intensive repairs.
- Assess Whether the Foundation is Newly Constructed or Requires Retrofitting: A newly constructed foundation may require less complex waterproofing systems, as it’s free from damage or previous treatments. However, older foundations that need retrofitting may require more robust solutions, such as sheet membranes or elastomeric coatings, to handle existing damage and increased water infiltration risks.
Match the Material to the Water Exposure Risk
The level of water exposure your foundation faces is one of the most important factors when selecting a waterproofing material. Different materials offer varying degrees of protection depending on the environment and water table level.
- High Water Table: For foundations in areas with a high water table or frequent groundwater pressure, choose materials like sheet membranes or bentonite. These systems provide an extra layer of protection against water infiltration, making them ideal for below-grade foundations and areas prone to flooding.
- Low Water Table: If your foundation is in an area with a low water table and minimal water exposure, more cost-effective solutions like cementitious or liquid-applied membranes may be sufficient. These materials offer reliable moisture protection without the need for the heavy-duty capabilities of other systems.
- Heavy Rainfall Areas: For regions with frequent heavy rainfall, elastomeric coatings or liquid-applied membranes are the best options. These materials provide flexibility and durability, ensuring that the foundation remains protected from water while accommodating movement or temperature changes.
Consider Installation Requirements
The type of waterproofing material you choose also depends on whether you plan to install it yourself or hire a professional. Some materials require specialized skills and equipment, while others are more DIY-friendly.
- Professional Installation: For large-scale projects or materials like sheet-based membranes, professional installation is usually recommended. Sheet membranes require precise application and sealing at the joints to ensure a watertight barrier, making professional expertise crucial to avoid leaks.
- DIY Installation: Smaller projects or interior applications can often be handled with DIY-friendly materials like liquid-applied membranes or cementitious coatings. These materials are easier to apply with basic tools and don’t require specialized skills, making them suitable for homeowners looking to waterproof a basement or crawl space.
Review Product Warranties and Longevity
When choosing a waterproofing material, it’s important to consider the product's warranty and expected lifespan. This can give you insight into the material’s durability and long-term effectiveness.
- Longer Warranties Usually Indicate Higher Durability: A longer warranty generally reflects a manufacturer’s confidence in the product’s performance. Materials with extended warranties, such as elastomeric coatings or sheet membranes, tend to be more durable and offer better protection over time.
- Factor in the Maintenance Schedule and Reapplication: Some waterproofing materials require regular maintenance or reapplication to remain effective. Liquid-applied membranes and cementitious coatings may need to be reapplied every few years, while more robust systems like bentonite or sheet membranes often last longer with less maintenance. Understanding the reapplication schedule is key to ensuring long-term protection for your foundation.
By following these steps, you can select the most appropriate waterproofing material for your foundation, ensuring that your home or building remains protected from water damage for years to come. Careful evaluation of your foundation’s condition, water exposure, and installation needs, as well as reviewing warranties and product longevity, will help you make the best decision for lasting protection.
Steps to Properly Apply Foundation Waterproofing Materials
Applying foundation waterproofing materials is essential to protecting your home or building from water damage and ensuring long-term durability. Whether you're using liquid-applied membranes, sheet membranes, or cementitious coatings, following the proper steps for surface preparation, application, and maintenance is crucial. Below is a comprehensive guide to help you apply foundation waterproofing materials effectively.
Surface Preparation
Before applying any waterproofing material, it's vital to ensure that the foundation surface is properly prepared. A clean, dry, and smooth surface is key to the success of any waterproofing system, as it allows the material to adhere properly and form a watertight barrier.
- Clean the Foundation Walls of Dirt, Dust, and Debris: Start by thoroughly cleaning the foundation walls. Use a wire brush, pressure washer, or stiff broom to remove any dirt, dust, debris, or loose particles. This ensures that the waterproofing material bonds directly to the foundation without obstructions.
- Repair Cracks and Surface Imperfections: Inspect the foundation for cracks, gaps, or surface irregularities. Repair any significant cracks using a suitable patching compound or filler before applying waterproofing material. This step is crucial for preventing water from seeping through imperfections in the foundation.
- Ensure the Surface is Dry and Free from Any Standing Water: Water or moisture on the surface can interfere with the adhesion of the waterproofing material. Ensure that the foundation is completely dry before applying the waterproofing system. Avoid applying the material right after rain or in high-humidity conditions.
Application Techniques by Material Type
Different waterproofing materials require specific application techniques to ensure they perform effectively. Below are guidelines for applying various types of waterproofing materials.
Liquid-Applied Membranes:
- Use a brush, roller, or sprayer to apply liquid-applied membranes in thin, even coats. Multiple layers are typically required for optimal protection, allowing each coat to dry fully before applying the next.
- Focus on achieving complete coverage, especially in hard-to-reach areas like corners and joints, to ensure no water can penetrate the surface.
Sheet Membranes:
- Secure sheet membranes using adhesive, ensuring they are applied smoothly without wrinkles or air pockets. Overlap seams by several inches to prevent leaks, and seal the joints using appropriate seam tape or adhesive to maintain a watertight barrier.
- Pay special attention to corners and edges, ensuring the membrane is properly adhered to avoid potential leaks.
Cementitious Coatings:
- Mix the cementitious waterproofing material according to the manufacturer's instructions. Apply it using a trowel or brush in an even layer, ensuring full coverage. These coatings typically cure into a rigid barrier that helps protect the foundation from water infiltration.
- This method is best suited for interior foundations or basement walls.
Elastomeric Coatings:
Apply elastomeric coatings with a roller or sprayer, making sure to cover the entire surface with an even layer. These flexible coatings are ideal for areas prone to movement, such as those experiencing temperature fluctuations or ground shifts. Ensure that cracks or gaps are fully covered to maintain a continuous, watertight membrane.
Final Inspection and Maintenance
Once the waterproofing material has been applied, it's important to inspect the work and maintain the system over time to ensure its long-term effectiveness.
- Inspect Regularly for Any Signs of Wear, Damage, or Leaks: After installation, regularly inspect the foundation for any visible signs of wear, damage, or leaks, particularly after heavy rain or extreme weather conditions. Pay close attention to the seams of sheet membranes or any areas where cracks could develop.
- Perform Necessary Repairs Quickly to Prevent Further Damage: If you notice any damage or wear, address it immediately. Small cracks or areas of damage can worsen over time if left untreated, leading to larger issues and potential water infiltration.
- Follow Manufacturer Instructions for Reapplication Intervals: Each type of waterproofing material has specific maintenance and reapplication intervals. Be sure to follow the manufacturer's guidelines to maintain optimal protection. Some materials, like liquid-applied membranes, may need reapplication every few years, while more durable materials like sheet membranes and elastomeric coatings may last longer with minimal maintenance.
By following these steps for surface preparation, proper application, and regular maintenance, you can ensure that your foundation is fully protected against water damage. Using the right techniques for each waterproofing material will help extend the life of your foundation and reduce the need for costly repairs in the future.
Why Waterproofing Your Foundation is Essential
Waterproofing is one of the most critical steps in the construction or renovation of any foundation. Foundations are constantly exposed to moisture and hydrostatic pressure from surrounding soil, which can lead to significant damage over time if not properly protected. Here are some key reasons why waterproofing your foundation is essential for maintaining the structural integrity and long-term safety of your home or building.
- Prevents Water Seepage and Cracks Due to Hydrostatic Pressure: One of the primary reasons for waterproofing is to protect against water infiltration caused by hydrostatic pressure. This pressure builds up when groundwater accumulates around the foundation, pushing moisture into cracks and weak points. Without proper waterproofing, this seepage can lead to cracks, weakening the foundation over time.
- Avoids Mold and Mildew, Protecting Indoor Air Quality: Moisture that seeps into a foundation can quickly lead to mold and mildew growth, which not only damages your property but also poses serious health risks. By waterproofing your foundation, you prevent moisture from entering your basement or crawl spaces, keeping indoor air clean and reducing the risk of respiratory problems.
- Protects the Foundation from Freeze-Thaw Cycles: In colder climates, the freeze-thaw cycle can cause water inside foundation cracks to expand and contract, further weakening the structure. Waterproofing helps protect the foundation from this cycle by preventing water from entering in the first place, reducing the risk of cracks and structural damage caused by temperature fluctuations.
- Reduces Long-Term Maintenance and Repair Costs: Waterproofing your foundation is an investment that pays off in the long run by minimizing the need for costly repairs. A properly waterproofed foundation reduces the likelihood of water damage, mold, and structural weakening, helping you avoid expensive and time-consuming restoration work in the future.
Understanding the Risks of Not Waterproofing a Foundation
Failing to waterproof a foundation properly can lead to a range of serious issues that affect both the structural integrity of your home and your health. Below are some of the major risks you face if your foundation is not adequately waterproofed.
- Water Infiltration Leading to Cracks and Structural Instability: Without waterproofing, water can seep into the foundation through small cracks or weak spots, gradually expanding and causing significant damage. Over time, these cracks can grow larger, leading to structural instability that compromises the safety of the entire building.
- Basement Flooding and Water Damage to Stored Items: A poorly waterproofed foundation increases the risk of basement flooding during heavy rains or when groundwater levels rise. This can result in water damage to valuable items stored in the basement and create an ongoing need for cleanup and repairs.
- Health Risks from Mold and Mildew Buildup: Moist environments are ideal breeding grounds for mold and mildew, both of which can grow rapidly if moisture is allowed to penetrate your foundation. Mold spores can affect indoor air quality and pose health risks, especially for individuals with allergies or respiratory conditions. By waterproofing your foundation, you help prevent mold growth and the associated health hazards.
- Increased Repair and Restoration Costs: Water damage doesn’t just affect the foundation; it can spread to other parts of your home, leading to costly repairs. In some cases, extensive water damage can require foundation repairs, mold remediation, and even structural reinforcement—all of which could have been avoided with proper waterproofing.
Waterproofing your foundation is a crucial step in ensuring the safety, durability, and longevity of your home. By preventing water infiltration, you protect your property from structural damage, health risks, and costly repairs, making waterproofing a wise long-term investment.
FAQs
Recent Blog Posts
Crawl Space News
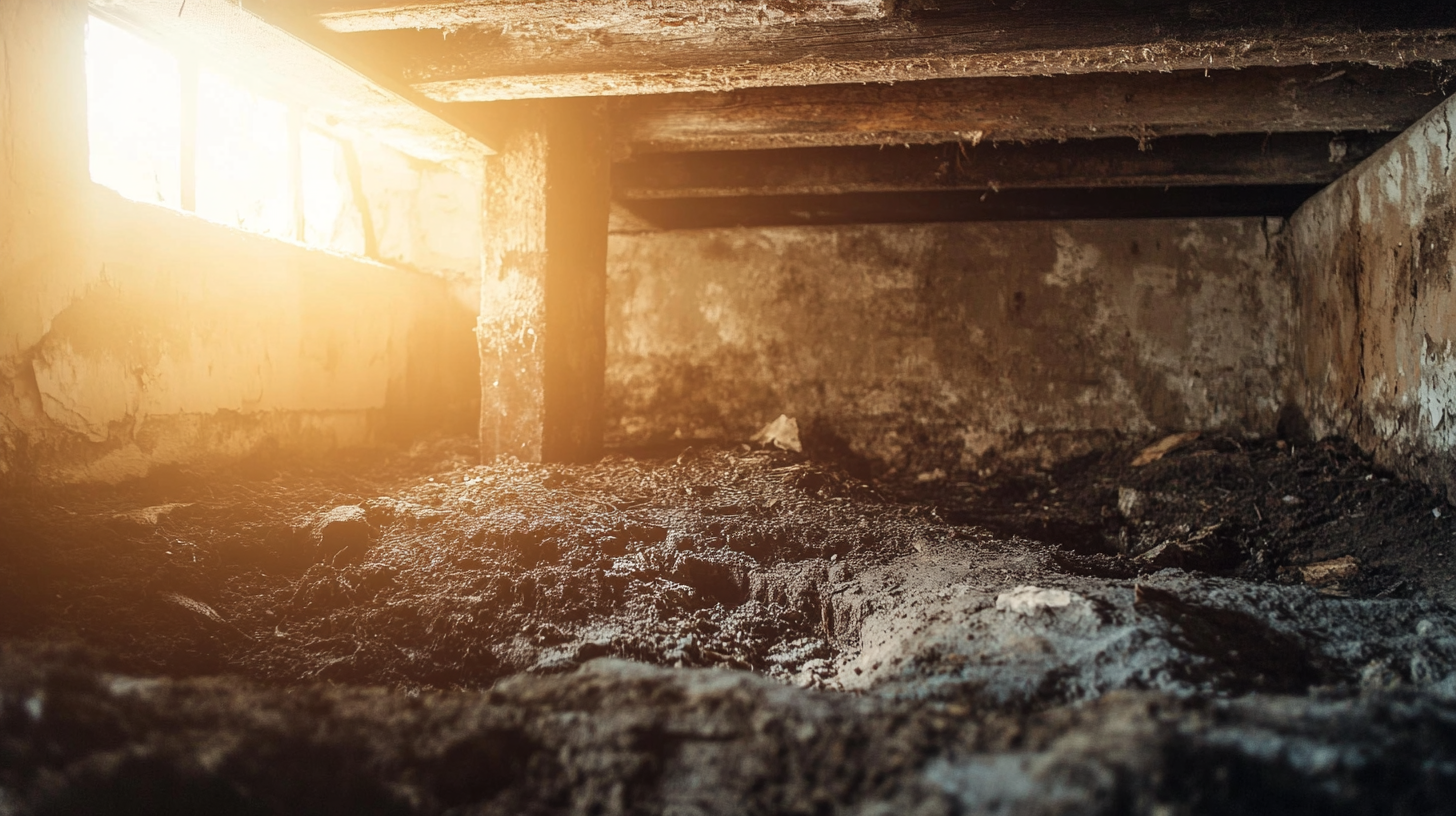
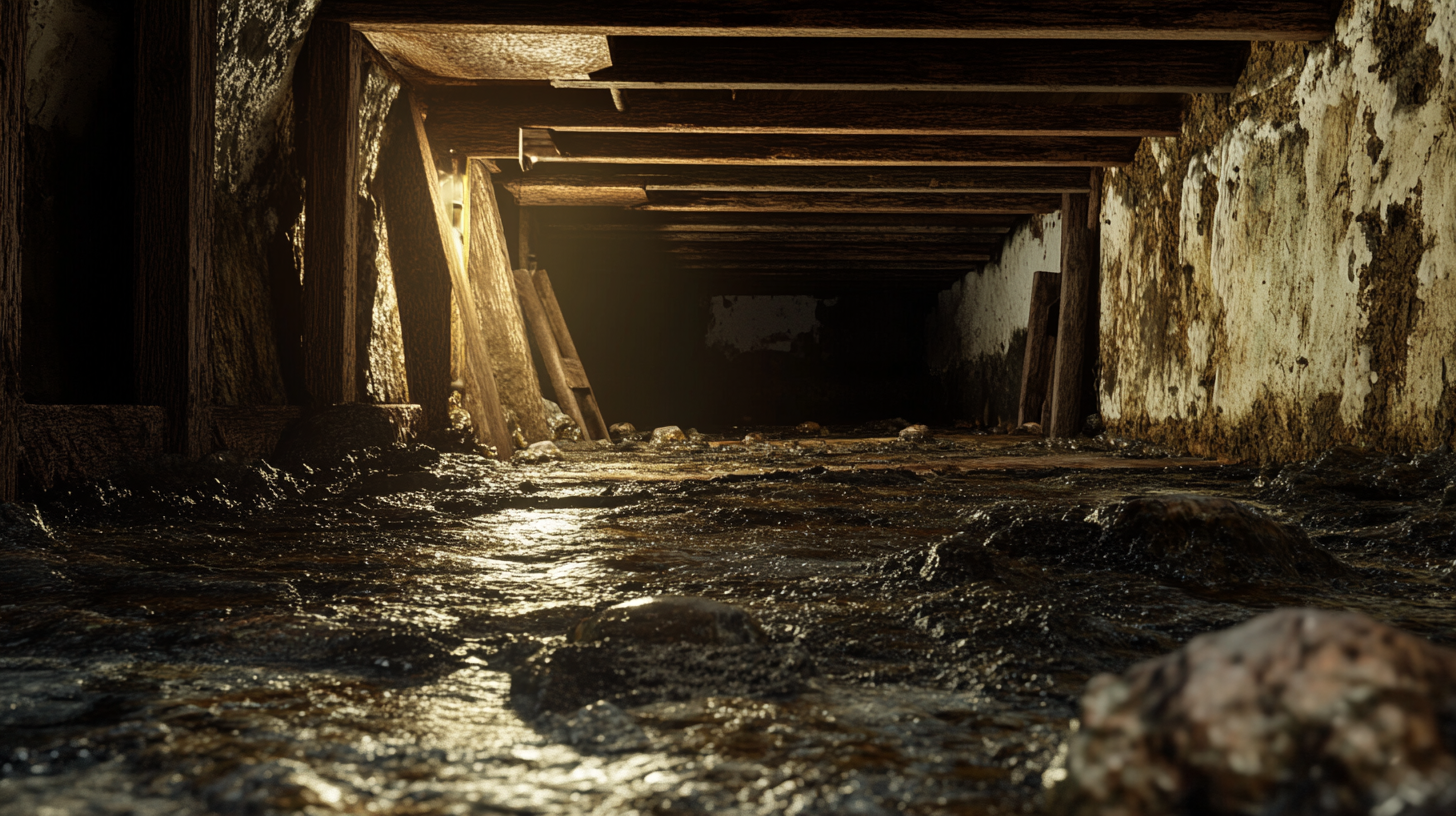
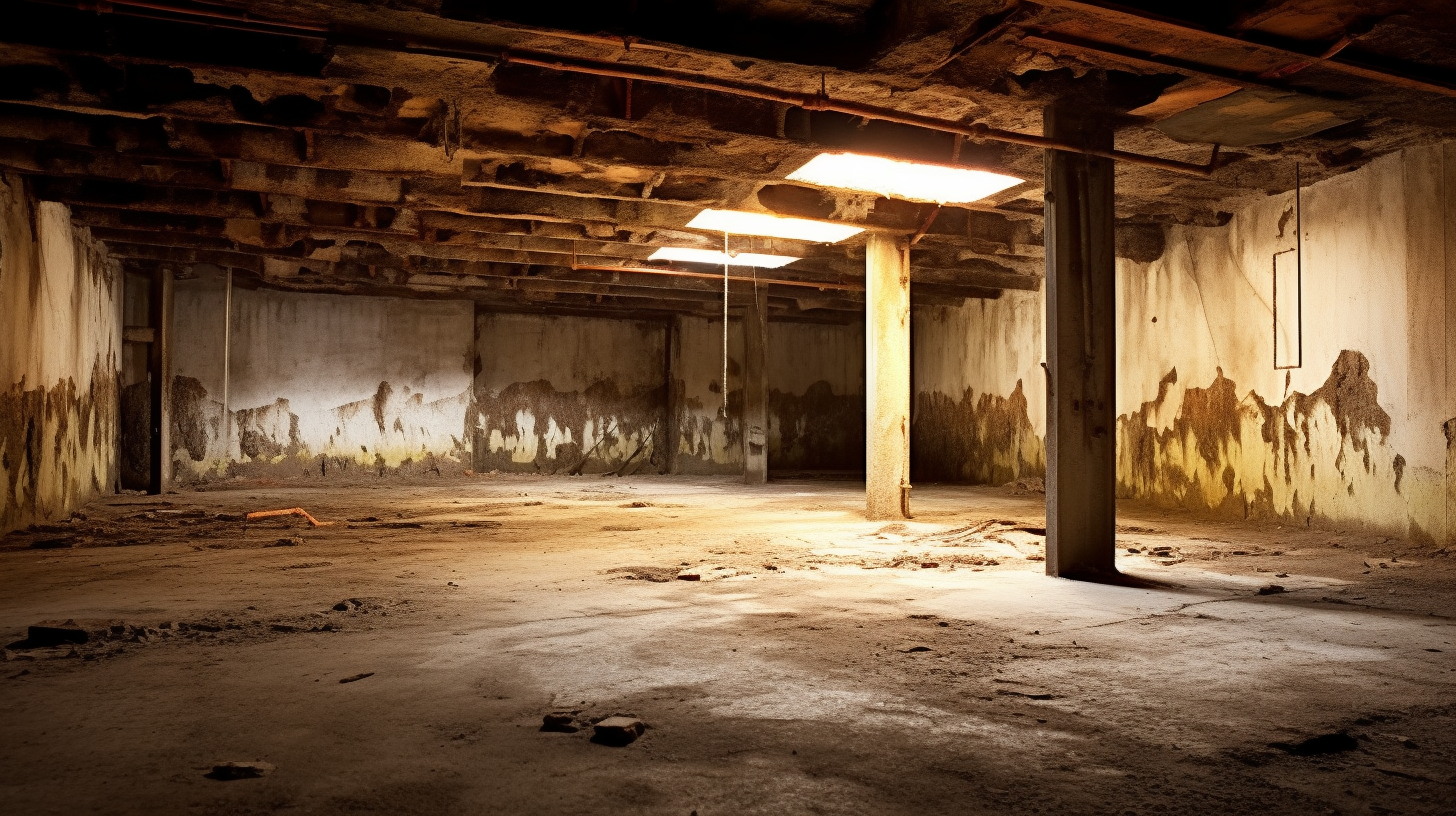