Now IS THe Time To...

Crawl Space Services In Knoxville, TN
Stetson Howard: 865-432-6743
CRAWL SPACE ENCAPSULATION, REPAIR, WATERPROOFING & MOLD REMOVAL
No-Obligation, Free Inspections
No-Obligation Free Estimates
We Warranty All of Our Work
100% Satisfaction Guaranteed
The stability of a building's foundation is crucial for its overall structural integrity and safety. A well-maintained foundation ensures that the entire structure remains level, secure, and capable of withstanding various environmental stresses. Neglecting foundation maintenance can lead to severe consequences, including significant structural damage, safety hazards, and costly repairs.
Foundation stability is influenced by several factors, such as soil conditions, weather patterns, and the quality of the original construction. Over time, these factors can contribute to the deterioration of the foundation, causing issues like cracks in walls and floors, uneven or sloping floors, and doors or windows that stick. Recognizing and addressing these problems early is essential for preventing minor issues from escalating into major structural failures.
The importance of maintaining foundation stability extends beyond the physical structure of the building. A stable foundation protects the property value and ensures the safety and comfort of its occupants. Additionally, with the increasing impact of climate change, which brings more frequent and severe weather events, proactive foundation maintenance is more critical than ever.
In this blog post, we will delve into the key aspects of foundation maintenance, explore common signs of foundation problems, and discuss practical measures for ensuring long-term stability. By understanding the importance of a stable foundation, homeowners and property managers can take proactive steps to protect their investments and ensure the longevity of their buildings.
Understanding Foundation Cracks and Their Causes
Foundation cracks are a common concern for homeowners and property managers, as they can indicate underlying issues that may compromise the structural integrity of a building. Understanding the causes and types of foundation cracks is essential for proper diagnosis and repair.
Common Causes of Foundation Cracks
Several factors can contribute to the development of foundation cracks. Identifying these causes helps in preventing further damage and implementing appropriate repair strategies:
- Soil Movement and Settlement: Soil movement is a primary cause of foundation cracks. Expansive soils, which swell with moisture and shrink when dry, can exert significant pressure on foundations. Over time, this movement can lead to cracks as the foundation settles unevenly. Soil settlement occurs when the ground beneath the foundation compresses or erodes, resulting in uneven support and stress on the structure.
- Hydrostatic Pressure from Water Buildup: Water accumulation around the foundation can create hydrostatic pressure, pushing against the foundation walls. This pressure can cause cracks, particularly in areas with poor drainage. Persistent water buildup weakens the foundation material, making it more susceptible to cracking and other forms of damage.
- Poor Construction Practices: Foundations that are not built to code or using substandard materials are more prone to cracking. Inadequate reinforcement, improper soil preparation, and insufficient curing time for concrete can all contribute to structural weaknesses. Poor construction practices can lead to early deterioration and increased vulnerability to environmental factors.
- Temperature Fluctuations and Freeze-Thaw Cycles: Temperature changes cause expansion and contraction of foundation materials. In colder climates, freeze-thaw cycles are particularly damaging. Water that seeps into cracks and then freezes expands, widening the cracks and causing further damage. Repeated cycles of freezing and thawing can exacerbate the problem, leading to significant structural issues over time.
Types of Foundation Cracks
Foundation cracks come in various forms, each indicating different underlying issues. Understanding the types of cracks helps in assessing the severity and necessary repairs:
- Hairline Cracks: Hairline cracks are thin, minor cracks that often appear as the foundation settles slightly over time. These cracks are typically not a cause for immediate concern but should be monitored for any changes or widening, which could indicate a more serious issue.
- Vertical and Horizontal Cracks: Vertical cracks are common and usually result from minor settling. While they can indicate some movement, they are often less serious than horizontal cracks. Horizontal cracks, on the other hand, can be a sign of significant pressure against the foundation walls, often due to hydrostatic pressure or soil movement. These cracks require prompt attention to prevent further damage.
- Diagonal Cracks: Diagonal cracks typically indicate differential settling, where one part of the foundation settles more than another. These cracks can vary in severity and may require professional evaluation to determine the underlying cause and appropriate repair.
- Structural vs. Non-Structural Cracks: Structural cracks are serious and affect the integrity of the building. They are usually wider than non-structural cracks and may be accompanied by other signs of foundation problems, such as sticking doors or windows. Non-structural cracks, while unsightly, do not compromise the foundation's stability and are often due to minor settling or shrinkage of materials.
Introduction to Carbon Fiber Reinforcement
Carbon fiber reinforcement is an advanced method used in foundation repair, offering several advantages over traditional materials. This section provides an overview of what carbon fiber is and why it is increasingly used for foundation repairs.
What is Carbon Fiber?
Carbon fiber is a strong and lightweight material made from thin strands of carbon atoms. Here are its key characteristics:
- Composition and Properties of Carbon Fiber: Carbon fiber is composed of carbon atoms bonded together in a crystalline formation. This structure gives it remarkable strength and rigidity. The fibers are often combined with other materials to form a composite that is lightweight and extremely strong.
- Strength-to-Weight Ratio and Durability: Carbon fiber boasts an exceptionally high strength-to-weight ratio, making it much stronger and lighter than traditional materials like steel. This property is particularly beneficial in construction and foundation repair, where structural strength and minimal weight are crucial.
- Resistance to Corrosion and Environmental Factors: Unlike steel, carbon fiber is resistant to corrosion, rust, and environmental degradation. It can withstand exposure to moisture, chemicals, and extreme temperatures, ensuring long-term durability and performance in various conditions.
Why Use Carbon Fiber for Foundation Repairs?
Carbon fiber offers several advantages that make it an ideal choice for foundation repairs:
- Advantages Over Traditional Materials (Steel, Epoxy): Compared to traditional materials like steel and epoxy, carbon fiber provides superior strength without adding significant weight. It is also less prone to corrosion and deterioration, making it a more durable and long-lasting solution.
- Non-Intrusive and Minimally Invasive Installation: The installation of carbon fiber reinforcement is minimally invasive. It involves applying strips or sheets directly to the foundation surface, avoiding the need for extensive excavation or structural alterations. This makes the repair process quicker and less disruptive.
- Long-Term Performance and Reliability: Carbon fiber reinforcement offers excellent long-term performance, maintaining its strength and integrity over time. It effectively stabilizes foundations, prevents further damage, and ensures the structural reliability of the building.
Applications of Carbon Fiber in Foundation Repair
Carbon fiber is versatile and can be used in various foundation repair applications. This section explores its use in reinforcing cracked walls, stabilizing bowing or leaning walls, and preventing water infiltration.
Reinforcing Cracked Walls
Carbon fiber is highly effective in reinforcing cracked walls, ensuring their stability and preventing further damage:
- Application Process for Carbon Fiber Strips or Sheets: The process involves cleaning the wall surface, applying a high-strength epoxy resin, and then adhering carbon fiber strips or sheets over the cracks. This creates a strong bond that reinforces the wall structure.
- Ensuring Proper Adhesion to the Foundation Surface: Proper adhesion is critical for the effectiveness of carbon fiber reinforcement. The surface must be prepared correctly, and the epoxy must be applied uniformly to ensure a strong, lasting bond between the carbon fiber and the wall.
- Enhancing Wall Strength and Preventing Further Cracking: Once applied, carbon fiber significantly enhances the strength of the wall. It distributes stress more evenly, reducing the likelihood of further cracking and maintaining the structural integrity of the foundation.
Stabilizing Bowing or Leaning Walls
Carbon fiber can also be used to stabilize walls that are bowing or leaning, providing a robust and discreet solution:
- Using Carbon Fiber to Reinforce and Straighten Walls: Carbon fiber strips or sheets can be applied vertically or horizontally to stabilize bowing or leaning walls. This reinforcement helps straighten the walls and prevents further movement.
- Installation Techniques for Vertical and Horizontal Support: The installation process varies depending on whether vertical or horizontal support is needed. Vertical strips are typically used for walls bowing inward, while horizontal strips can address lateral pressure and leaning.
- Benefits of Carbon Fiber Over Traditional Bracing Methods: Compared to traditional bracing methods like steel braces, carbon fiber is less intrusive and does not require significant alterations to the wall structure. It provides effective support without compromising the aesthetics of the building.
Preventing Water Infiltration
Carbon fiber can also play a role in preventing water infiltration, which is critical for maintaining foundation integrity:
- Combining Carbon Fiber with Waterproofing Solutions: Carbon fiber can be used in conjunction with waterproofing solutions to create a comprehensive barrier against moisture. This combination ensures that the foundation remains dry and stable.
- Sealing Cracks to Prevent Moisture Penetration: Applying carbon fiber over cracks and using waterproof epoxy can seal the foundation against water penetration. This prevents moisture from entering the foundation, reducing the risk of water damage and mold growth.
- Enhancing the Overall Integrity of the Foundation: By preventing water infiltration and reinforcing the structure, carbon fiber enhances the overall integrity of the foundation. This ensures long-term stability and protects the building from environmental factors.
Installation Process for Carbon Fiber Reinforcement
The installation process for carbon fiber reinforcement involves several critical steps to ensure the effectiveness and durability of the repair. This section outlines the preparation, application, and final inspection stages.
Preparation and Surface Cleaning
Proper preparation and surface cleaning are essential for ensuring the carbon fiber material adheres correctly and performs effectively:
- Inspecting the Crack and Surrounding Area: Begin by thoroughly inspecting the crack and the surrounding area to assess the extent of the damage. This inspection helps determine the appropriate repair strategy and identify any additional structural issues that need to be addressed.
- Cleaning the Surface to Ensure Proper Adhesion: Clean the surface around the crack meticulously to remove dirt, dust, oil, and any loose particles. This step is crucial because a clean surface ensures better adhesion of the epoxy and carbon fiber material, which is vital for the success of the repair.
- Repairing Minor Cracks and Surface Defects: Before applying the carbon fiber, repair any minor cracks and surface defects using an appropriate filler or sealant. This step helps create a smooth, even surface, which enhances the bonding of the carbon fiber material and improves the overall durability of the repair.
Applying the Carbon Fiber Material
The application of carbon fiber involves precise measurement, cutting, and positioning to ensure maximum effectiveness:
- Measuring and Cutting Carbon Fiber Strips or Sheets: Measure the area to be reinforced and cut the carbon fiber strips or sheets to the required size. Accurate measurement and cutting are essential to ensure that the material covers the entire crack and provides adequate reinforcement.
- Mixing and Applying the Epoxy Adhesive: Mix the epoxy adhesive according to the manufacturer’s instructions to achieve the correct consistency and strength. Apply the epoxy uniformly over the prepared surface, ensuring it penetrates any cracks and provides a strong bonding layer for the carbon fiber material.
- Positioning and Securing the Carbon Fiber Material: Position the carbon fiber strips or sheets over the epoxy-coated area and press them firmly into place. Ensure that the material is correctly aligned and adheres fully to the surface. Use a roller or similar tool to remove any air bubbles and ensure complete contact between the carbon fiber and the epoxy.
Curing and Final Inspection
The final stage involves allowing the epoxy to cure properly and conducting a thorough inspection to ensure the quality of the reinforcement:
- Allowing Sufficient Time for the Epoxy to Cure: Allow the epoxy to cure for the time specified by the manufacturer. This curing period is crucial for the epoxy to harden and form a strong bond with the carbon fiber and the foundation surface.
- Inspecting the Reinforcement for Proper Adhesion and Coverage: After the epoxy has cured, inspect the reinforced area to ensure that the carbon fiber is properly adhered and fully covers the crack. Look for any signs of incomplete bonding or coverage that may need attention.
- Making Any Necessary Touch-Ups or Adjustments: If the inspection reveals any areas where the carbon fiber has not adhered correctly or where additional coverage is needed, perform the necessary touch-ups or adjustments. This step ensures the repair is complete and the foundation is fully reinforced.
Benefits of Carbon Fiber Reinforcement
Carbon fiber reinforcement offers numerous advantages for foundation repair, making it an increasingly popular choice for enhancing structural integrity. This section explores the key benefits, focusing on strength, durability, and the non-intrusive installation process.
Strength and Durability
Carbon fiber is renowned for its exceptional strength and durability, making it ideal for reinforcing foundations:
- Superior Strength-to-Weight Ratio: Carbon fiber has an outstanding strength-to-weight ratio, surpassing that of traditional materials like steel. This means that it provides robust reinforcement without adding significant weight to the structure, which is crucial for maintaining the foundation's stability without overloading it.
- Long-Lasting Performance with Minimal Maintenance: One of the significant advantages of carbon fiber is its longevity. Once installed, carbon fiber reinforcement requires minimal maintenance, providing a long-lasting solution that resists environmental factors such as moisture, temperature fluctuations, and chemical exposure. This durability ensures that the foundation remains stable and secure for many years, reducing the need for frequent repairs or replacements.
Non-Intrusive Installation
The installation process for carbon fiber reinforcement is designed to be minimally invasive, offering several practical benefits:
- Minimal Disruption to the Property and Occupants: Unlike traditional repair methods that may require extensive excavation or structural alterations, carbon fiber reinforcement is applied directly to the existing foundation surface. This approach significantly reduces disruption to the property and its occupants, allowing homeowners to continue their daily routines with minimal inconvenience.
- Quick Installation Process Compared to Traditional Methods: The application of carbon fiber reinforcement is relatively quick and straightforward. Once the surface is prepared and cleaned, carbon fiber strips or sheets are adhered using epoxy resin. The curing process is rapid, allowing the reinforcement to be completed in a shorter timeframe compared to traditional methods like underpinning or installing steel braces. This efficiency translates to faster project completion and less downtime for the property.
FAQs
Recent Blog Posts
Crawl Space News
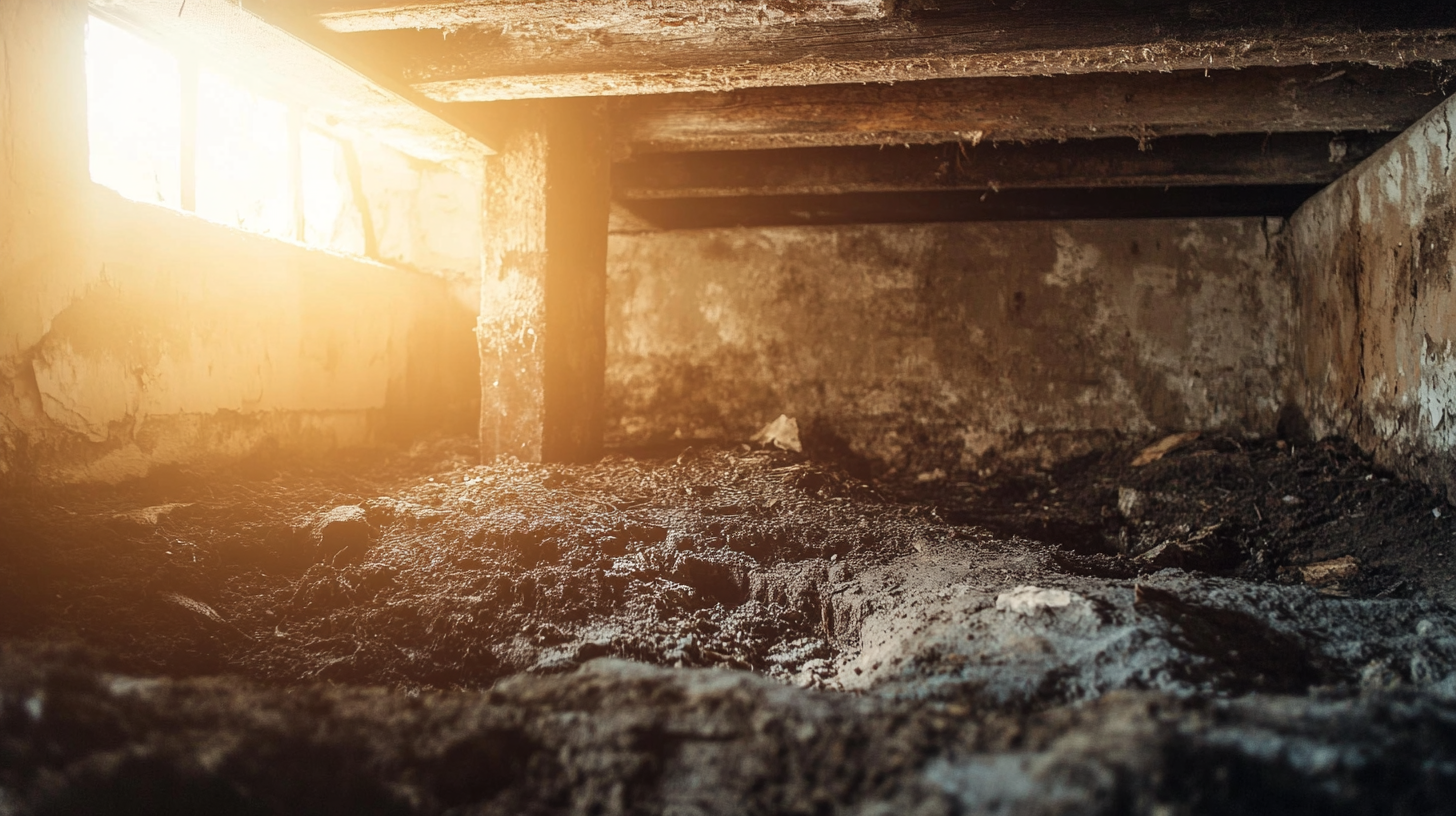
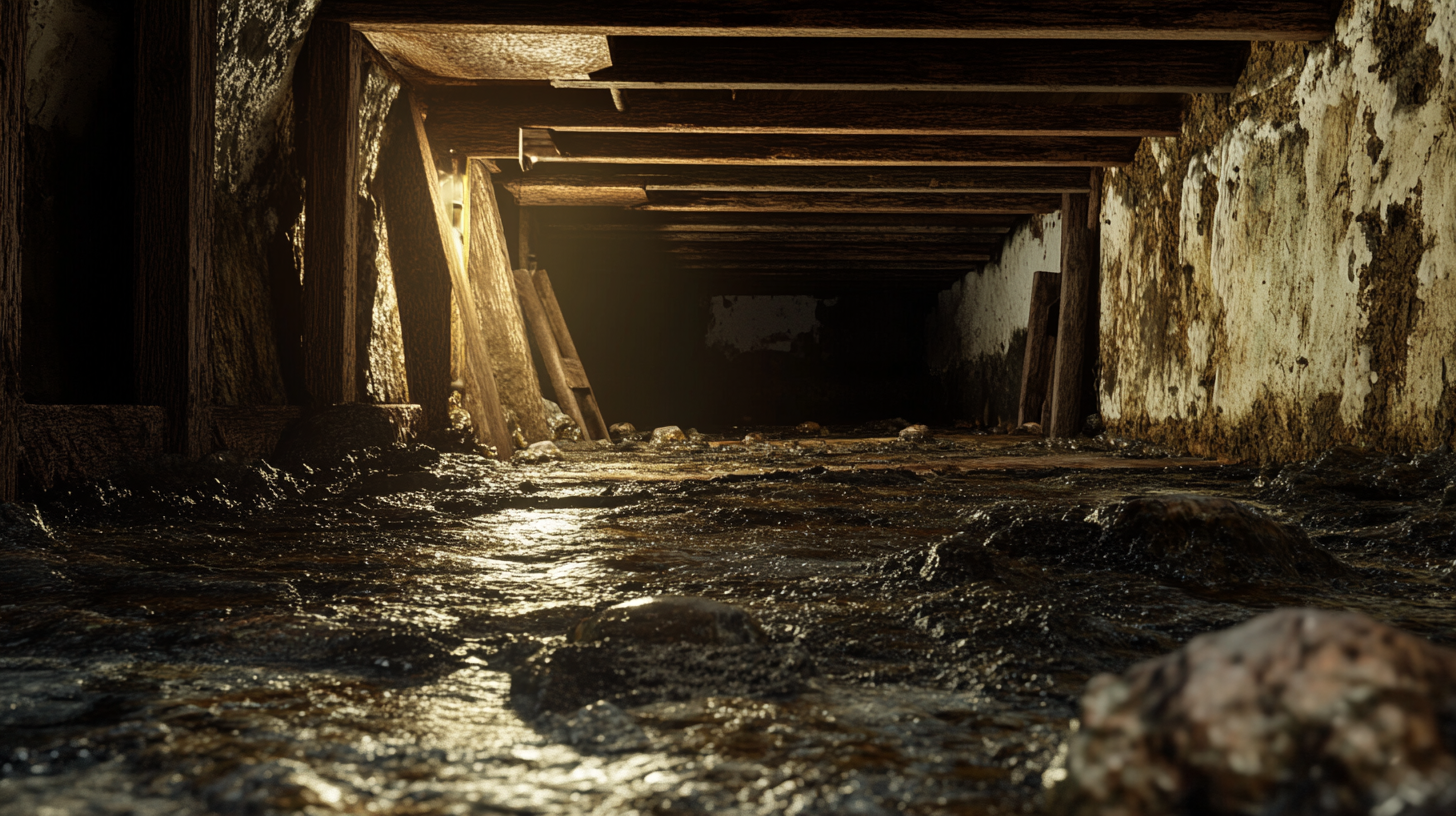
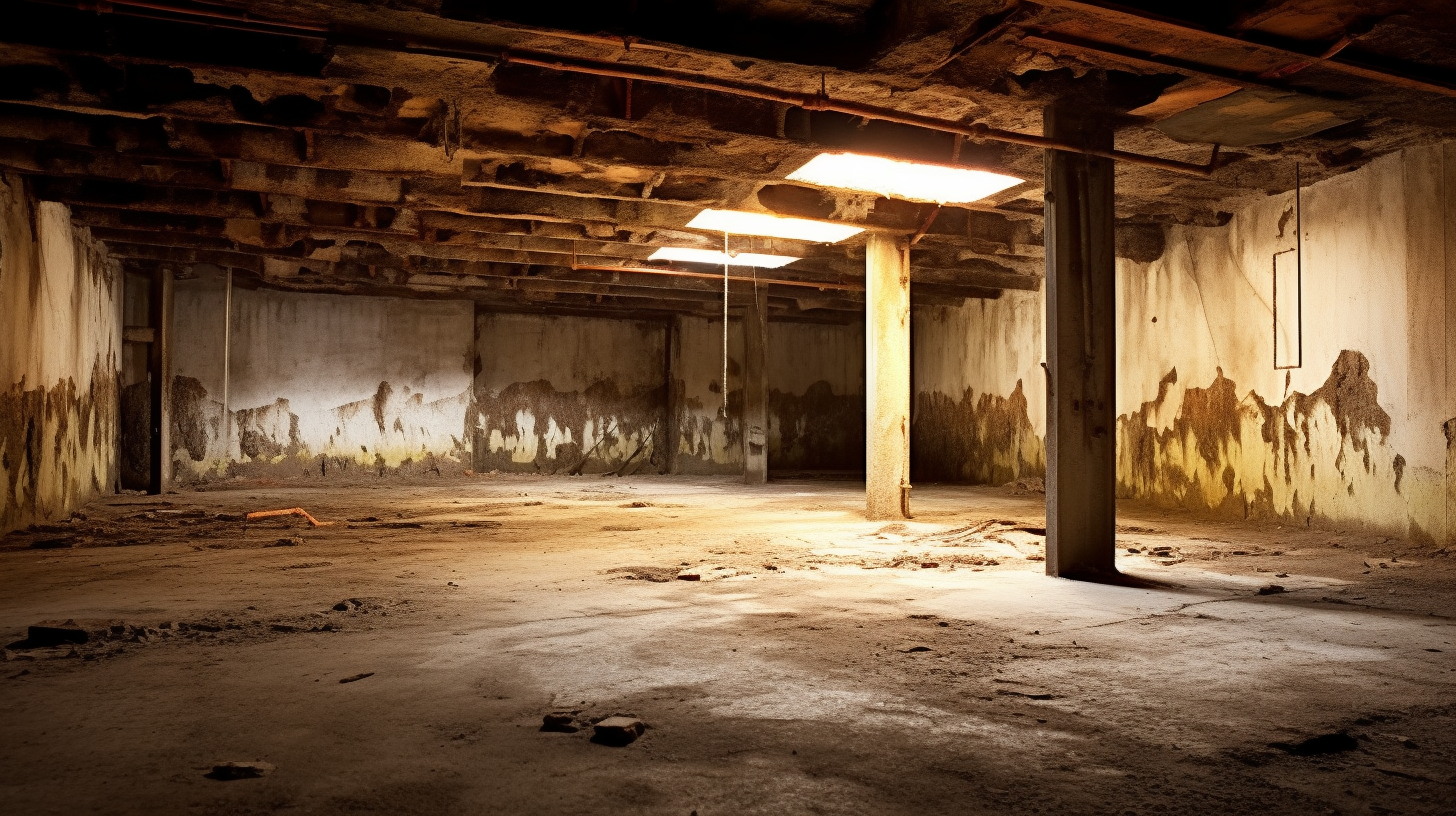