Now IS THe Time To...

Crawl Space Services In Knoxville, TN
Stetson Howard: 865-432-6743
CRAWL SPACE ENCAPSULATION, REPAIR, WATERPROOFING & MOLD REMOVAL
No-Obligation, Free Inspections
No-Obligation Free Estimates
We Warranty All of Our Work
100% Satisfaction Guaranteed
Below-grade waterproofing refers to the process of protecting structures that are built below ground level, such as basements, foundations, and underground parking areas, from water infiltration. These areas are particularly vulnerable to water pressure from surrounding soil, groundwater, and rainfall, which can lead to serious structural damage, mold growth, and long-term maintenance issues if not properly addressed.
The importance of below-grade waterproofing cannot be overstated, as it ensures the integrity and longevity of a building’s foundation by preventing water-related issues. Effective waterproofing solutions help avoid costly repairs and safeguard the structural health of the building, making them a critical aspect of construction, especially in areas prone to high water tables or heavy rainfall. In this blog, we will explore the fundamentals of below-grade waterproofing, why it matters, and the best practices for ensuring long-lasting protection.
Understanding Below-Grade Waterproofing
Below-grade waterproofing is a specialized practice designed to protect structures built below ground level from water infiltration. These systems are essential for ensuring the structural integrity and longevity of areas like basements, foundations, tunnels, and retaining walls, which are constantly exposed to groundwater pressure and varying soil conditions. A well-designed waterproofing system prevents water from penetrating the building’s foundation, helping to avoid structural damage, mold growth, and costly repairs.
What is Below-Grade Waterproofing?
Definition: Below-grade waterproofing refers to waterproofing solutions specifically designed for areas located below ground level, such as basements, foundation walls, and underground tunnels. These systems form a protective barrier that prevents groundwater from infiltrating the structure, keeping it dry and stable.
Typical Applications: Below-grade waterproofing is commonly used in:
- Basements and foundation walls, where water infiltration can weaken the structure and cause mold growth.
- Tunnels and underground parking structures, where constant exposure to groundwater poses a significant risk of water damage.
- Retaining walls, which hold back soil and water, making them vulnerable to leaks and cracks if not properly protected.
Importance of Groundwater Protection: One of the most critical functions of below-grade waterproofing is to prevent groundwater infiltration. When water enters below-ground structures, it can create hydrostatic pressure, pushing against foundation walls. Without adequate protection, this pressure can lead to cracks, leaks, and even structural failure. By managing hydrostatic pressure and using effective waterproofing materials, these risks can be significantly minimized.
Challenges of Below-Grade Waterproofing
Hydrostatic Pressure: One of the biggest challenges in below-grade waterproofing is hydrostatic pressure, which occurs when groundwater pushes against a structure's foundation. This pressure can increase significantly after heavy rainfall or snowmelt, forcing water into cracks or weak points in the waterproofing system. Properly designed waterproofing systems must account for this pressure to prevent structural damage and water infiltration.
Moisture Migration: Moisture migration refers to the movement of water through the soil and into foundation walls. Over time, even small amounts of water can seep through porous materials, leading to mold growth, concrete deterioration, or internal leaks. Below-grade waterproofing must be continuous and durable to block moisture migration and maintain the building’s structural health.
Soil Conditions: Different soil types, such as clay or sand, can have a significant impact on water behavior and waterproofing needs. Clay soils tend to retain water, increasing hydrostatic pressure on the structure, while sandy soils allow water to flow more freely, reducing pressure but potentially creating drainage issues. An effective below-grade waterproofing system takes into account the specific soil conditions at the site, ensuring the appropriate waterproofing solution is applied.
Temperature Extremes: Below-grade areas are subject to freezing and thawing cycles, which can cause water in the soil to expand and contract. This process can create cracks in foundation walls and damage waterproofing membranes if they are not flexible enough to handle these temperature changes. It is critical to choose waterproofing materials that are durable and elastic enough to withstand these extreme temperature fluctuations.
Key Considerations When Choosing Below-Grade Waterproofing Materials
Selecting the right waterproofing materials for below-grade structures is critical for ensuring long-term protection against water infiltration. Several factors, such as the type of structure, site conditions, and the durability of materials, play a significant role in determining the most effective waterproofing solution. Each project is unique, and understanding these key considerations will help ensure that the chosen materials can withstand environmental pressures and protect the structure over its lifespan.
Type of Structure and Usage
Residential vs. Commercial: The waterproofing needs of residential and commercial buildings can differ significantly. Residential homes may require less intensive waterproofing solutions, focusing primarily on basement walls and foundations. In contrast, large commercial buildings or infrastructure projects—such as tunnels or parking garages—often face higher water pressure and have greater exposure to environmental stressors, requiring more robust waterproofing materials. For example, commercial structures often need materials that can handle higher levels of hydrostatic pressure and greater durability due to higher foot traffic and mechanical loads.
Substructure Depth: The depth of the below-grade structure is another critical consideration. Deeper foundations and substructures are more likely to experience increased hydrostatic pressure from surrounding groundwater. As the depth increases, the risk of water infiltration also grows, meaning more robust waterproofing systems are necessary to resist the higher pressure and potential for leaks. Deep structures often benefit from multi-layered waterproofing systems or more advanced solutions like bentonite clay or HDPE (High-Density Polyethylene) membranes.
Site Conditions
Groundwater Levels: One of the most important factors to evaluate is the groundwater level at the building site. Sites with high water tables or areas prone to flooding require waterproofing materials that provide stronger water resistance to prevent groundwater from seeping into the structure. Materials such as liquid-applied membranes, which form a seamless barrier, or heavy-duty sheet membranes are ideal for these conditions, as they offer excellent water-tightness even under high pressure.
Soil Type: The soil composition surrounding the structure also impacts the choice of waterproofing materials. Clay soils, for example, tend to retain water, trapping moisture against the foundation and increasing hydrostatic pressure. This can necessitate more impermeable waterproofing solutions. On the other hand, sandy soils offer better natural drainage, reducing the pressure on the waterproofing system, but still requiring a durable material to protect against water seepage. Understanding the site's soil type allows for the selection of a waterproofing material that effectively addresses the specific challenges posed by the environment.
Climate: Climate plays a significant role in determining the type of waterproofing materials needed for below-grade applications. In cold climates, materials that are freeze-thaw resistant are essential, as freezing water can expand and damage foundations and waterproofing membranes. Conversely, in warmer climates, it’s important to consider waterproofing systems that offer UV resistance, particularly for any portions of the system that may be exposed above ground or to occasional sunlight. Choosing climate-appropriate materials helps ensure long-lasting protection.
Material Durability and Lifespan
Longevity: Waterproofing materials should be chosen based on their expected lifespan and ability to perform without failure. The material must withstand environmental stressors such as water pressure, temperature changes, and movement over time. For long-term projects, investing in higher-quality materials that offer extended durability may reduce the need for frequent repairs and replacements, providing a better return on investment in the long run.
Resistance to Chemicals: In some cases, the soil or groundwater may contain aggressive chemicals or salts that can degrade certain waterproofing materials over time. Structures built in industrial areas or near bodies of saltwater need materials with chemical resistance to prevent deterioration. Waterproofing systems like PVC membranes or bentonite-based solutions are often chosen for their resilience against chemical attacks. Ensuring that the selected materials are capable of withstanding potential chemical exposure is crucial for maintaining the integrity of the waterproofing system over the years.
Types of Waterproofing Materials for Below-Grade Applications
Below-grade waterproofing requires specialized materials designed to withstand constant exposure to water and ground pressure. These materials form a barrier that prevents water infiltration, protecting structures from damage, mold growth, and weakening. Each type of waterproofing material offers unique advantages, and the choice of material depends on the specific needs of the project, including environmental conditions and structural requirements. Below are some common waterproofing materials used in below-grade applications.
Sheet Membranes
Self-Adhering Sheets:
Self-adhering sheet membranes are a popular choice for below-grade waterproofing, as they provide a strong, pre-applied or post-applied barrier against water. These membranes are typically made from modified bitumen or high-density polyethylene (HDPE), materials known for their water resistance and durability. Self-adhering sheets are especially effective for large, flat surfaces such as foundation walls. The sheets bond to the surface, creating a continuous barrier that prevents water penetration. While these membranes are relatively easy to install, they require precise handling to avoid damage during application, as tears or punctures can compromise their effectiveness.
Vulcanized Rubber Sheets:
Vulcanized rubber sheets are another versatile option for below-grade waterproofing, particularly in environments where flexibility is key. These sheets are extremely flexible, even in cold temperatures, making them ideal for regions with harsh winters. Their high elasticity allows them to stretch and accommodate building movement and small cracks that may develop over time. Vulcanized rubber sheets provide reliable waterproofing protection and can maintain their integrity even in challenging conditions.
Liquid-Applied Membranes
Polyurethane Membranes:
Polyurethane membranes offer a seamless, flexible solution for below-grade waterproofing. These liquid-applied systems are highly adaptable, making them ideal for surfaces with complex shapes or detailed architectural features. The membranes provide high flexibility and excellent crack-bridging capabilities, allowing them to handle structural movement without losing their waterproofing effectiveness. However, these systems often require multiple coats to ensure full protection, which can increase installation time and costs.
Cementitious Coatings:
Cementitious coatings are among the easiest waterproofing materials to apply, typically with a brush or roller. These coatings are durable and can be used for both positive side (external) and negative side (internal) waterproofing, making them versatile for a range of below-grade applications. While cementitious coatings are less flexible than other options like polyurethane membranes, they are highly durable and can withstand significant wear over time. Their ease of application makes them a go-to choice for waterproofing projects where flexibility is less of a concern.
Bentonite Clay Waterproofing
Sodium Bentonite Sheets:
Sodium bentonite is a natural clay material that expands when it comes into contact with water, forming a tight seal that blocks water infiltration. Sodium bentonite sheets are often used in areas with fluctuating water tables, as the clay’s self-sealing properties allow it to fill cracks and voids in the foundation. This makes bentonite an excellent option for environments where groundwater pressure varies. However, repeated wetting and drying cycles can cause bentonite to degrade over time, which may require additional maintenance or replacement in areas with extreme environmental conditions.
Crystalline Waterproofing Systems
Integral Crystalline Waterproofing:
Crystalline waterproofing systems offer a unique approach by becoming an integral part of the concrete structure itself. These systems are applied as a coating or added as an admixture to the concrete during the construction process. Once applied, the crystals grow inside the concrete, blocking water pathways and sealing cracks as they develop. This system’s self-healing properties allow it to respond to future cracks, which can significantly extend the lifespan of the concrete. Integral crystalline waterproofing is especially effective in new construction projects, but it requires accurate application to ensure the crystals form properly and create the necessary waterproof barrier.
Pros and Cons of Below-Grade Waterproofing Materials
Selecting the right waterproofing material for below-grade applications involves weighing the benefits and potential drawbacks of each option. Every material has unique properties that make it more suitable for specific environments and structural requirements. Below, we examine the pros and cons of common below-grade waterproofing materials, helping you determine which solution is best suited for your project.
Sheet Membranes
Pros:
- Uniform thickness and controlled installation: Sheet membranes provide consistent, uniform thickness across the entire surface, ensuring reliable waterproofing.
- Durable and resistant: These membranes are built to withstand various environmental factors, such as water pressure, UV exposure, and fluctuating temperatures, making them a durable choice for below-grade applications.
- Suitable for large surfaces: Sheet membranes are ideal for large, flat surfaces such as foundation walls and retaining structures, offering a strong barrier against water infiltration.
Cons:
- Vulnerable to punctures or tears: During installation, sheet membranes can be easily punctured or torn, which can compromise their waterproofing capability. Careful handling is required to prevent damage.
- Requires skilled labor: The application of sheet membranes, particularly at joints and edges, demands precision and expertise. Skilled labor is necessary to ensure proper sealing and installation, which can increase costs.
Liquid-Applied Membranes
Pros:
- Seamless application: Liquid-applied membranes form a seamless barrier, which significantly reduces the risk of water leakage, particularly at joints and penetrations.
- Flexible and adaptable: These membranes are highly flexible and can easily conform to complicated details and irregular shapes, making them suitable for a variety of below-grade structures with complex geometries.
- Ideal for irregular surfaces: Liquid-applied systems are perfect for structures with irregular shapes or surfaces that are difficult to cover with pre-formed materials.
Cons:
- Weather-sensitive application: The effectiveness of liquid-applied membranes can be impacted by weather conditions such as temperature and humidity. Application in the wrong conditions may result in improper curing or reduced effectiveness.
- Requires several coats: To achieve full waterproofing protection, liquid-applied membranes usually require multiple coats, which can extend the application time and increase labor costs.
Bentonite Clay Waterproofing
Pros:
- Natural and eco-friendly: Bentonite clay is a natural, environmentally friendly waterproofing material, making it a sustainable choice for green building projects.
- Self-sealing capabilities: Bentonite has a unique ability to self-seal when it comes into contact with water, effectively filling cracks and voids in the foundation.
- Can be applied on uneven surfaces: Unlike some other materials, bentonite does not require a smooth surface for application, making it versatile in a variety of conditions.
Cons:
- Prone to degradation: Bentonite is susceptible to degradation when exposed to continuous wetting and drying cycles, which can reduce its long-term effectiveness.
- Affected by chemical-laden groundwater: In some environments, groundwater containing salts or other chemicals can impair the performance of bentonite, leading to reduced waterproofing capability.
Crystalline Waterproofing
Pros:
- Self-healing and long-lasting: Crystalline waterproofing systems offer self-healing properties, with crystals growing to seal cracks over time. This extends the lifespan of the system and reduces the need for frequent maintenance.
- Versatile application: Crystalline waterproofing can be used for both positive side (external) and negative side (internal) waterproofing, making it adaptable for various below-grade applications.
- Resistant to chemicals: These systems are highly resistant to chemical attack, making them suitable for structures exposed to aggressive environments or contaminated groundwater.
Cons:
- Limited flexibility: Crystalline waterproofing lacks flexibility, making it less suitable for structures that experience large structural movement or significant shifts over time.
- Requires precise application conditions: For the best results, crystalline waterproofing must be applied under specific conditions, requiring careful monitoring to ensure proper crystal formation and waterproofing performance.
Choosing the Right Waterproofing Material for Your Below-Grade Project
Selecting the appropriate waterproofing material for a below-grade project is essential to ensure long-term protection against water infiltration. The choice of material should be based on various factors, including the nature of the project, the environmental conditions, and the structural demands of the building. Below, we explore the key considerations that will guide you in choosing the best waterproofing solution for your below-grade structure.
Assessing Project Needs
New Construction vs. Retrofit: The type of project—whether new construction or a retrofit of an existing structure—plays a significant role in material selection. For new builds, you may have greater flexibility in choosing advanced waterproofing systems that can be integrated during the initial construction phase, such as integral crystalline waterproofing or pre-applied sheet membranes. For retrofits, where accessibility may be limited, liquid-applied membranes or post-applied sheet systems are often more practical due to their adaptability to existing conditions. Understanding the project’s stage will help you choose a solution that fits seamlessly with your construction or renovation plan.
Exposure to Water: It is crucial to determine the level of water exposure your below-grade structure will face. Areas with high water pressure or frequent exposure to groundwater may require heavy-duty materials such as sodium bentonite sheets or high-density polyethylene (HDPE) membranes that can withstand intense hydrostatic pressure. In contrast, for areas with lower water exposure, a simpler system like cementitious coatings may suffice. Assessing the hydrostatic pressure and water infiltration risk at your site is essential for selecting a waterproofing material that will provide the necessary protection.
Building Movement: Structures that are prone to settling or movement, such as those built on shifting soils or areas with seismic activity, require flexible waterproofing materials. Options like EPDM or polyurethane membranes are highly elastic and can adapt to cracks or shifts without losing their waterproofing integrity. Selecting materials with high flexibility will ensure the system continues to perform even as the building undergoes natural movements.
Installation Factors
Professional Installation: One of the most important factors in the success of any below-grade waterproofing system is professional installation. Even the best materials can fail if not applied correctly. For materials like sheet membranes, precise handling and proper sealing at joints and edges are critical. Similarly, liquid-applied membranes require even and consistent application to form a seamless barrier. Engaging experienced professionals who understand the complexities of below-grade waterproofing will help ensure that the system is installed correctly and functions as intended.
Curing Time: Some waterproofing materials, particularly liquid-applied systems, require adequate curing time to achieve their full waterproofing potential. For example, polyurethane membranes may need several hours or even days to fully cure, depending on the environmental conditions and the number of coats applied. It is important to account for curing time in the project timeline to avoid compromising the performance of the waterproofing system.
Weather Conditions: The weather during installation can significantly affect the performance of certain waterproofing materials. Liquid-applied membranes, for instance, are sensitive to temperature and humidity levels and may not cure properly if applied in unfavorable weather conditions. For areas prone to rain or extreme temperature fluctuations, it may be necessary to schedule the installation during periods of optimal weather or choose materials that are less dependent on environmental conditions, such as sheet membranes.
Maintenance and Long-Term Performance
Ease of Repair: Over time, even the most durable waterproofing systems may require repairs due to wear, movement, or unexpected damage. When selecting a material, consider how easy it is to repair in the event of a failure. Sheet membranes can often be patched at damaged areas, while liquid-applied systems may require reapplication in specific spots. Materials that are easier to repair can save time and money in the long run, especially in high-risk environments where ongoing maintenance is expected.
Regular Inspections: Ensuring the long-term performance of your waterproofing system involves conducting regular inspections. Routine checks help catch small issues, such as cracks or water infiltration, before they become major problems. Scheduling regular inspections, particularly after significant weather events or ground shifts, will help you maintain the effectiveness of your waterproofing solution and extend its lifespan. Proper maintenance is a critical part of any below-grade waterproofing strategy, regardless of the material used.
FAQs
Recent Blog Posts
Crawl Space News
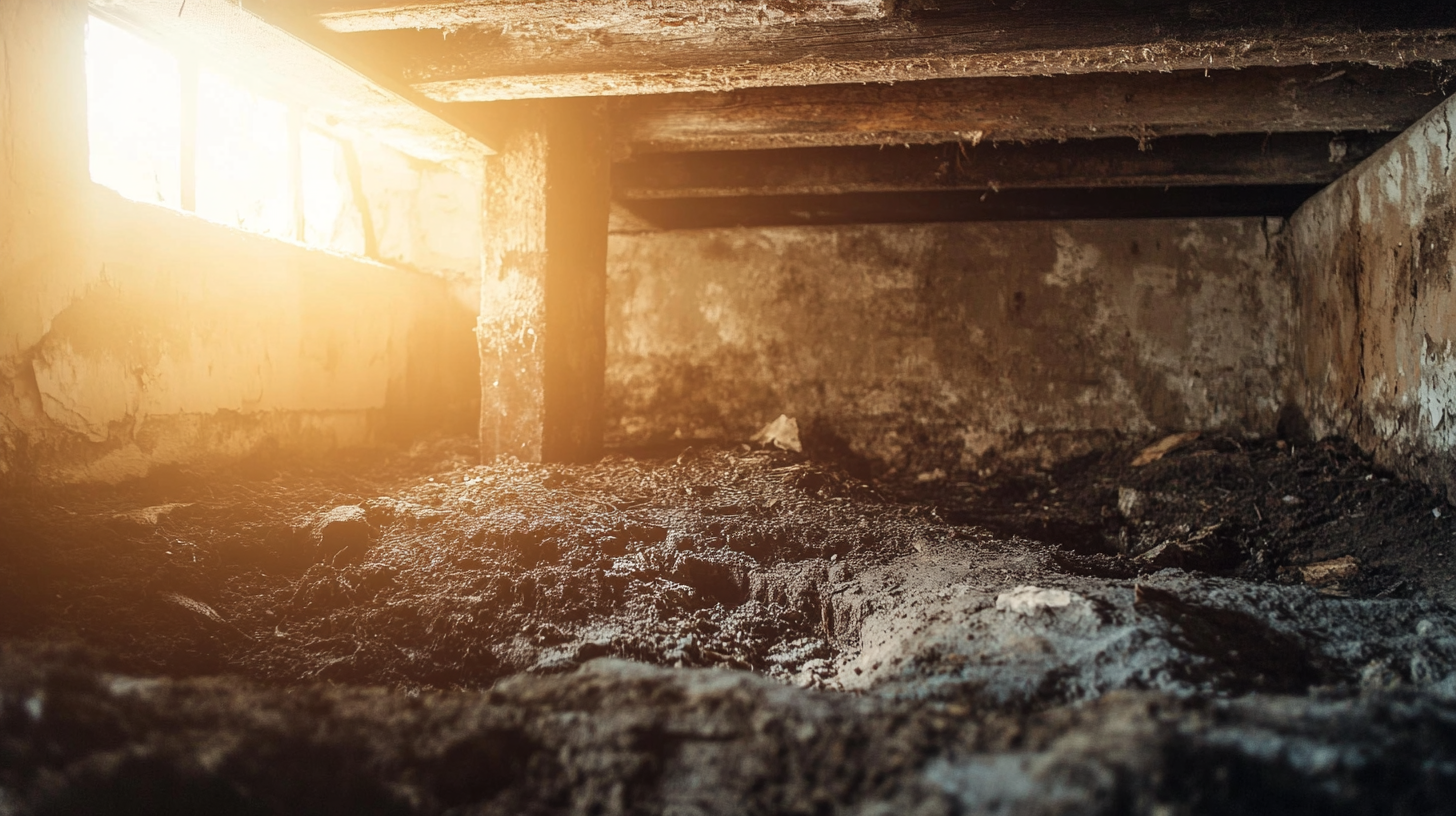
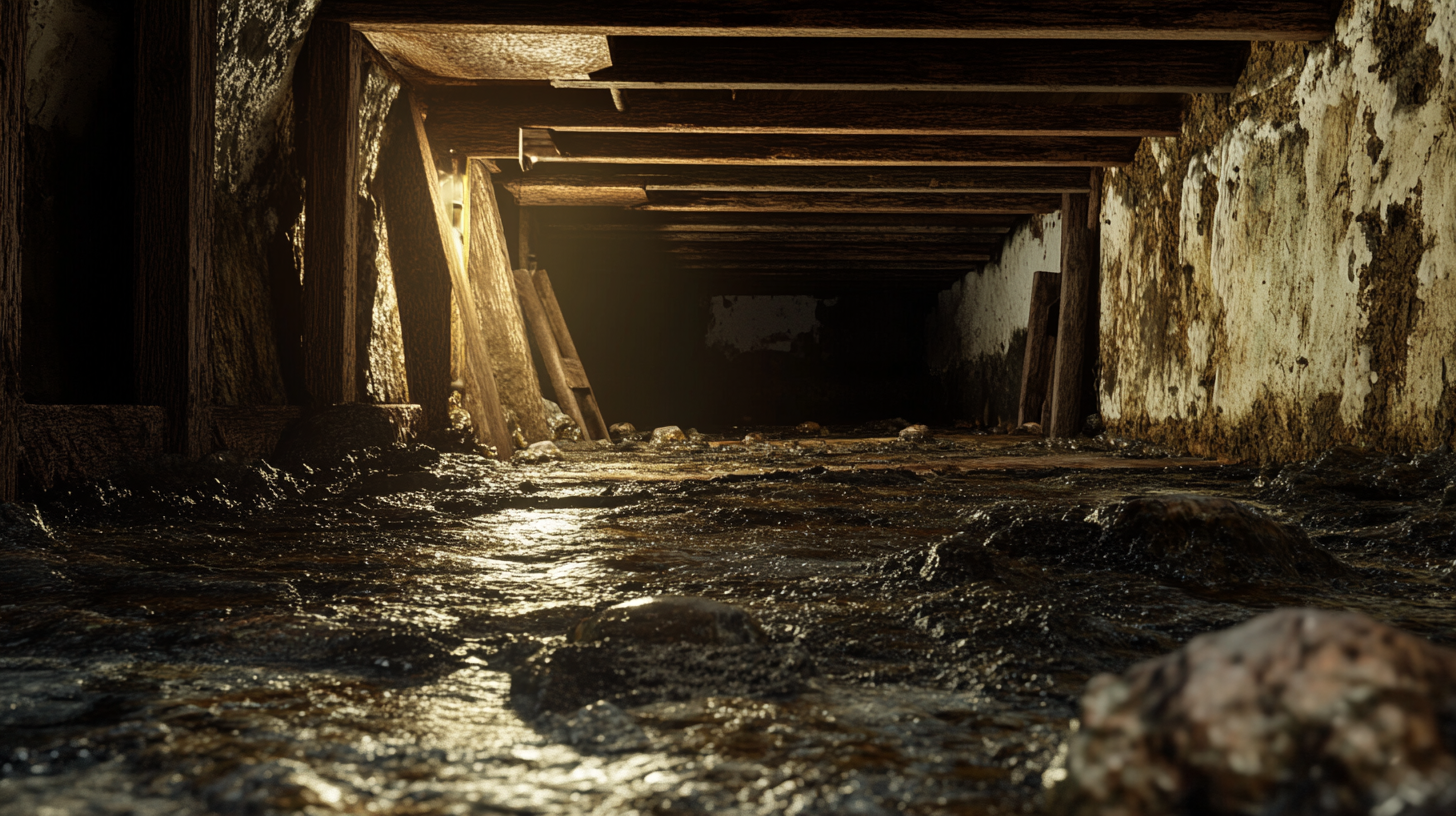
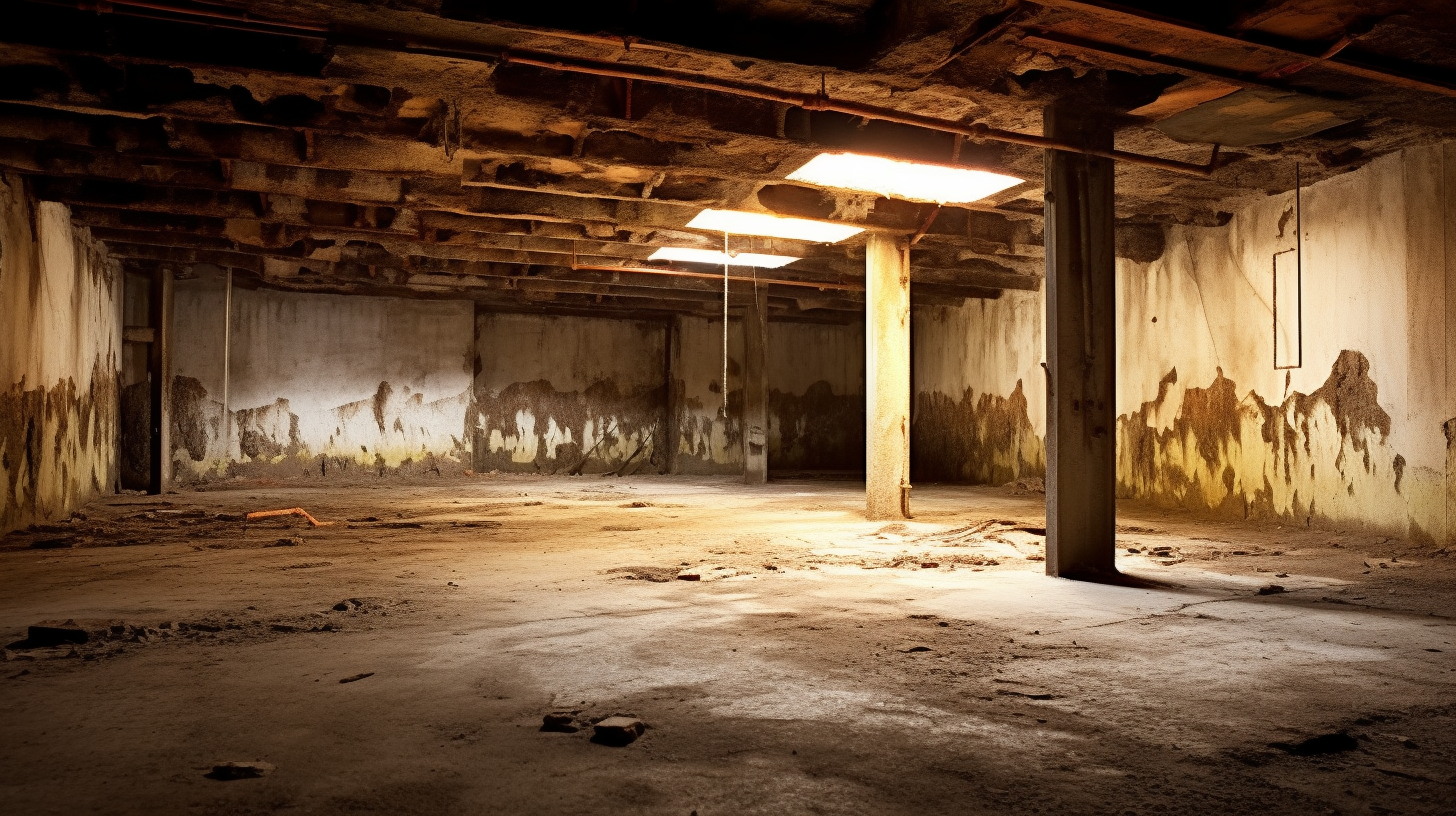