Now IS THe Time To...

Crawl Space Services In Knoxville, TN
Stetson Howard: 865-432-6743
CRAWL SPACE ENCAPSULATION, REPAIR, WATERPROOFING & MOLD REMOVAL
No-Obligation, Free Inspections
No-Obligation Free Estimates
We Warranty All of Our Work
100% Satisfaction Guaranteed
Flat roofs, popular in both residential and commercial construction, present unique challenges due to their design and constant exposure to the elements. Unlike sloped roofs that naturally shed water, flat roofs are more susceptible to issues such as ponding water, which can lead to leaks, structural damage, and premature wear if not properly addressed. These roofs also endure direct exposure to harsh weather conditions, including intense sunlight, heavy rainfall, snow, and fluctuating temperatures, all of which can compromise the integrity of the waterproofing systems in place.
In this blog, we will explore some of the most common problems flat roofs encounter, from drainage difficulties to material degradation, and offer insights into how these issues can be mitigated through effective design, material selection, and maintenance. Understanding these challenges is key to ensuring the long-term durability and performance of flat roofs.
Key Considerations in Choosing Waterproofing Solutions for Flat Roofs
Waterproofing is a critical process in construction that protects structures from water penetration, ensuring long-term durability and safety. Whether it’s used in foundations, roofs, or walls, a proper waterproofing system prevents water damage, mold, and structural weakening. Effective waterproofing systems are designed to prevent water from entering areas where it could cause damage, thereby extending the life of a building and maintaining its integrity. In this section, we will explore what waterproofing entails and delve into the most common types of systems used in modern construction.
What is Waterproofing?
Definition and Explanation of Waterproofing in Construction
Waterproofing in construction refers to the process of making a structure water-resistant, so that it remains impervious to moisture and liquid water. This protection is essential in areas such as basements, roofs, and foundations, where prolonged exposure to water can lead to deterioration. In essence, waterproofing acts as a barrier that prevents water from passing through and damaging materials, protecting both the structural elements and interior spaces from moisture-related issues such as decay, corrosion, and mold growth.
Common Types of Waterproofing Systems
Waterproofing systems vary depending on the specific needs of a project and the environment it will be exposed to. Some of the most widely used waterproofing methods include:
- Liquid Membranes: These are applied in a liquid state and cure to form a seamless, flexible membrane. Liquid membranes can conform to a variety of shapes and surfaces, providing excellent coverage and protection. They are commonly used in roofing and foundation applications.
- Sheet Membranes: Pre-fabricated sheets of waterproofing material are applied to the surface, typically in overlapping layers to ensure full coverage. These sheets are made from materials such as rubber or modified bitumen, offering a durable and reliable barrier against water.
- Cementitious Waterproofing: This type of waterproofing uses a cement-based product mixed with specific bonding agents and is often applied to areas like water tanks, basements, and bridges. It is known for its strength and ability to form a solid, watertight layer.
Key Components of a Waterproofing System
An effective waterproofing system is composed of several essential elements, each contributing to the overall performance of the barrier. These components must work together seamlessly to ensure the structure remains watertight.
- Membranes: As the primary barrier, membranes are the most critical component of any waterproofing system. Whether applied in liquid or sheet form, the membrane must provide continuous coverage and resist water penetration. Membranes are typically flexible and durable to accommodate any movement or settling of the structure without cracking or compromising the seal.
- Sealants and Adhesives: Sealants and adhesives are used to ensure a strong, waterproof bond between materials, particularly at joints, edges, or around penetrations (such as pipes or vents). These products play a vital role in maintaining the integrity of the waterproofing system by sealing gaps that could allow water to enter.
- Substrate: The substrate is the surface onto which the waterproofing system is applied. The condition of the substrate can significantly affect the performance of the waterproofing system. It must be clean, smooth, and properly prepared to ensure the membrane adheres effectively and forms a continuous barrier.
- Drainage Systems: Effective drainage is essential to manage water flow around the structure, especially in areas prone to heavy rain or groundwater accumulation. Proper drainage prevents water from accumulating and applying pressure on the waterproofing system, reducing the risk of leaks and structural damage over time.
Common Waterproofing Material Options for Flat Roofs
Choosing the right waterproofing material for flat roofs is essential to ensure long-term protection against water infiltration, UV damage, and the effects of fluctuating temperatures. Each material has its own unique strengths, making certain options more suitable for specific applications depending on the environment, structural needs, and maintenance requirements. In this section, we will explore some of the most common waterproofing materials used for flat roofs, from single-ply membranes to liquid-applied systems.
Single-Ply Membranes
EPDM (Ethylene Propylene Diene Monomer)
EPDM is one of the most widely used single-ply roofing membranes due to its high durability and flexibility. It is especially resistant to UV radiation, making it an ideal choice for areas with intense sunlight exposure. EPDM’s elasticity allows it to expand and contract with temperature changes, reducing the risk of cracks or tears. Additionally, this membrane has a long lifespan and requires minimal maintenance, making it a cost-effective option for long-term use on flat roofs.
TPO (Thermoplastic Olefin)
TPO membranes have become increasingly popular due to their UV resistance and energy-efficient properties. TPO is reflective, helping to reduce heat absorption and lower energy costs, particularly in warmer climates. The heat-weldable seams of TPO provide excellent waterproof protection by creating strong, watertight bonds. Its environmental benefits, such as being 100% recyclable, have made it a favorite for eco-conscious projects. TPO is durable and offers a long service life, making it a reliable choice for flat roofs.
PVC (Polyvinyl Chloride)
PVC membranes are known for their excellent resistance to chemicals, oils, and greases, making them an ideal option for commercial roofs with mechanical units or industrial activity. PVC is flexible and durable, with heat-welded seams that provide added waterproofing protection. Like TPO and EPDM, PVC is also UV-resistant and has a long lifespan, performing well under harsh environmental conditions. Its strength and resistance to punctures make it a top choice for roofs that experience heavy foot traffic.
Bituminous Membranes
SBS-Modified Bitumen
SBS-modified bitumen is a flexible, elastic material designed to handle fluctuating temperatures, making it ideal for climates where temperature changes are frequent. It can be applied using either hot or cold methods, depending on the needs of the project. SBS membranes are easy to repair, which contributes to their cost-effectiveness over the long term. Its flexibility allows it to adapt to structural movements, preventing cracks and maintaining a durable waterproof seal.
APP-Modified Bitumen
APP-modified bitumen is more rigid than SBS and offers greater resistance to heat, making it well-suited for high-temperature climates. It is applied using a torch to create a strong, durable bond with the roof surface, ensuring effective waterproofing. APP membranes are valued for their durability and long-lasting performance, especially in environments where exposure to heat and UV radiation is a concern. This type of bitumen provides excellent resistance to environmental stressors while maintaining a waterproof seal.
Liquid Waterproofing Systems
Liquid Polyurethane Membrane
Liquid polyurethane membranes offer a seamless, highly flexible, and durable solution for waterproofing flat roofs. This liquid-applied system is ideal for roofs with complex shapes and details, as it conforms to every surface it covers, creating an uninterrupted barrier against water. With excellent UV resistance and elongation properties, polyurethane membranes can handle extreme temperature fluctuations and are highly resistant to environmental damage. Their flexibility ensures that they can accommodate structural movement without compromising their waterproofing capabilities.
Liquid Rubber Membrane
Liquid rubber membranes are an environmentally friendly, water-based waterproofing solution suitable for both new roofs and repair projects. This liquid system provides a fully bonded, seamless finish, ensuring comprehensive coverage and protection against water penetration. Liquid rubber is known for its ability to handle structural movement effectively, making it a durable choice for flat roofs exposed to dynamic environmental conditions. Its ease of application and eco-friendly formulation make it an attractive option for sustainable construction practices.
Pros and Cons of Different Waterproofing Materials
When selecting waterproofing materials for flat roofs, it is important to weigh the advantages and disadvantages of each option to ensure the best performance and longevity for your specific project. Each material has unique properties that make it more suitable for certain environments and building requirements. In this section, we’ll explore the pros and cons of various common waterproofing materials to help you make an informed decision.
EPDM
Pros:
- Long lifespan (up to 50 years): EPDM is known for its exceptional durability, with some installations lasting for decades with minimal maintenance.
- Environmentally friendly and recyclable: EPDM is a sustainable choice, as it can be fully recycled at the end of its service life, reducing waste.
- Highly resistant to UV and ozone: Its chemical composition makes it highly resistant to UV radiation and ozone exposure, ensuring it performs well in sunny climates.
Cons:
- Dark color may absorb heat: EPDM’s dark surface can absorb heat, increasing cooling costs in warmer climates, especially when used in areas with high sun exposure.
- Requires specialized installation tools: The seams in EPDM systems require specialized tools and adhesives, making the installation process more complex.
TPO
Pros:
- White, reflective surface for energy efficiency: TPO’s reflective surface helps reduce heat absorption, lowering energy costs in warm climates.
- Environmentally friendly: TPO is fully recyclable, making it a popular choice for environmentally conscious projects.
- Economical: TPO membranes are often more cost-effective than other single-ply options, providing a balance of performance and affordability.
Cons:
- Less proven track record: While TPO has gained popularity, it doesn’t have the same long-established performance history as EPDM, which could be a consideration for long-term projects.
- Requires precise installation: The seams in TPO systems are heat-welded and require precision during installation to avoid potential seam failures.
PVC
Pros:
- Strong seams due to heat welding: PVC membranes have durable, heat-welded seams that provide excellent resistance to water infiltration.
- Great chemical and fire resistance: PVC is ideal for roofs exposed to industrial environments due to its resistance to chemicals and fire.
- Reflective, reducing energy costs: Like TPO, PVC has a reflective surface that helps reduce heat absorption and can lower cooling costs.
Cons:
- Can shrink over time: PVC membranes may shrink, especially under prolonged exposure to heat, which can lead to stress on seams and potential leaks.
- Higher cost: PVC is often more expensive than other single-ply membranes, which could impact budget considerations.
Bituminous Membranes
Pros:
- Durable, especially in harsh weather conditions: Bituminous membranes, particularly APP-modified bitumen, are known for their strength and durability, making them suitable for extreme weather.
- Low-cost option: These membranes offer an economical solution for long-term waterproofing, making them a popular choice for budget-conscious projects.
- Easy to install and maintain: Bituminous membranes are relatively straightforward to install and maintain, reducing long-term costs and complexity.
Cons:
- Can become brittle over time: Exposure to extreme temperatures can cause bituminous membranes to become brittle, increasing the risk of cracks.
- Requires careful installation with torches: APP-modified bitumen requires torch-applied installation, which demands skilled labor and safety precautions to avoid improper application.
Liquid Waterproofing Systems
Pros:
- Seamless, reducing the risk of water ingress: Liquid-applied systems create a seamless barrier, minimizing the likelihood of leaks through joints or seams.
- Flexible, ideal for complex shapes: Liquid membranes can easily adapt to irregular roof shapes and details, providing a versatile solution for complicated roof designs.
- Quick to install: Liquid systems often allow for faster installation with minimal disruption to the structure, which can be particularly advantageous in time-sensitive projects.
Cons:
Requires multiple coats: To achieve optimal waterproofing performance, liquid systems typically require several layers, which can increase application time and cost.
Shorter lifespan: Liquid waterproofing systems generally have a shorter lifespan compared to membrane-based systems, which might necessitate more frequent maintenance or replacement.
How to Choose the Right Waterproofing Material for Your Flat Roof
Choosing the right waterproofing material for your flat roof requires careful consideration of several factors, from the environmental conditions to your budget and long-term maintenance needs. Flat roofs, due to their design, face unique challenges, so selecting a material that can withstand the specific demands of your roof’s environment is essential to ensuring a long-lasting, effective waterproofing system.
Consider the Roof’s Environment
Climate: The local climate is one of the most important factors to consider when choosing a waterproofing material. If your building is located in a sunny area, opt for materials with high UV resistance like EPDM or TPO, which are designed to withstand prolonged sun exposure without degrading. For regions that experience extreme cold, materials that can handle temperature fluctuations and resist cracking in freezing conditions, such as SBS-modified bitumen, are more appropriate. Ensuring that the waterproofing system is well-suited to your climate will help prevent premature wear and extend the roof’s lifespan.
Roof Usage: The intended use of the roof is another key consideration. If the roof will be subject to foot traffic—such as for equipment storage or access for building maintenance—opt for materials that are more durable and puncture-resistant, like PVC or modified bitumen. These materials can handle the wear and tear associated with frequent use. If the roof is simply there to cover the building and won’t see much activity, a less robust material may be sufficient, but it should still meet the environmental requirements of the area.
Factor in Budget and Maintenance
Initial Cost vs. Long-Term Savings: When selecting a waterproofing material, it’s important to balance the initial cost with long-term savings. Some materials, like EPDM, may have a higher upfront cost but offer significant savings over time due to their low maintenance needs and long lifespan (up to 50 years in some cases). Other materials, such as bituminous membranes, may be more affordable initially but could require more frequent inspections and repairs. Assessing both the initial investment and maintenance costs will help you choose a solution that fits your budget while ensuring long-term performance.
Ease of Repair: No matter how durable a material is, all flat roofs will eventually require some form of maintenance or repair. Consider choosing a material that is easy to repair, like SBS-modified bitumen, which can be patched relatively quickly and cost-effectively. Materials that are easier to maintain or repair can help minimize downtime and reduce costs over the roof’s lifespan, making them a smart choice for buildings where accessibility or budget constraints are a concern.
Professional Installation Matters
Importance of Expert Installation: Even the best waterproofing materials can fail if they are not installed correctly. Professional installation is critical to ensuring that your waterproofing system performs as intended. Improperly applied seams, poor adhesion, or uneven application can lead to leaks and premature failures. Hiring experienced professionals who specialize in flat roof waterproofing systems—whether you choose TPO, PVC, or bituminous membranes—will ensure that the system is applied properly and according to the manufacturer’s specifications.
Maintenance: Once installed, regular inspections and prompt repairs are essential for extending the lifespan of your flat roof’s waterproofing solution. Professional contractors can identify potential issues early, such as cracks, ponding water, or seam failures, allowing you to address these problems before they cause significant damage. Routine maintenance will not only prolong the life of the roof but also help avoid costly repairs that result from neglected issues.
Factors to Consider for Long-Term Performance of Flat Roof Waterproofing
The long-term performance of a flat roof’s waterproofing system depends on various factors that must be considered when selecting materials and planning installation. Climate, maintenance needs, and budget considerations all play critical roles in ensuring that the waterproofing solution remains effective for years. By evaluating these key aspects, you can make informed decisions that contribute to the durability and functionality of your flat roof system.
Climate and Environmental Conditions
UV Exposure: One of the most significant factors impacting the lifespan of flat roof waterproofing is UV exposure. In regions with intense sunlight, materials like TPO and PVC are highly recommended due to their reflective properties. These membranes not only resist UV degradation but also help reduce heat absorption, which can lower cooling costs for the building. Their ability to reflect sunlight makes them ideal for roofs in hot, sunny climates where excessive heat can cause less UV-resistant materials to deteriorate prematurely.
Temperature Extremes: For areas with large temperature fluctuations, where summers are hot and winters are freezing, EPDM stands out as an excellent choice. Its flexibility allows it to expand and contract without cracking or losing adhesion, making it suitable for both hot and cold environments. This resilience ensures that EPDM can maintain its waterproofing integrity despite repeated thermal cycling, offering long-term durability in extreme climates.
Maintenance and Inspection
Routine Inspections: The effectiveness of a flat roof’s waterproofing system heavily relies on routine inspections. Regular roof checks allow property owners to spot early signs of wear or damage, such as small cracks, ponding water, or loose seams. Identifying these issues early ensures that repairs can be made before they lead to more extensive damage. Scheduling periodic inspections—especially after severe weather events—can significantly extend the life of the waterproofing system and prevent costly failures.
Repairability: Some waterproofing materials are easier to repair than others, and repairability is a key factor in maintaining long-term performance. Liquid-applied membranes, for example, are simple to patch and repair, as they can be reapplied directly over damaged areas to create a seamless finish. In contrast, sheet membranes, like TPO or PVC, may require seam re-welding to ensure a watertight repair, which can be more complex and labor-intensive. Understanding how easily a system can be maintained and repaired is essential for keeping the roof in optimal condition.
Budget and Cost Considerations
Upfront vs. Long-Term Costs: When choosing a waterproofing system, it's important to balance upfront costs with long-term savings. Systems like PVC and TPO may have a higher initial cost, but they offer energy savings due to their reflective properties, which reduce cooling expenses in hot climates. Additionally, these materials are highly durable, which means they may require less frequent maintenance and repairs, ultimately saving money over the roof’s lifetime. Considering both the initial investment and the potential for long-term savings is key to selecting a cost-effective solution.
Cost of Professional Installation: Another crucial factor to consider is the cost of professional installation. Some waterproofing systems, such as modified bitumen, require specialized installation methods, like torch application, which can increase labor costs due to the need for skilled professionals. While these systems may be durable and effective, it’s essential to factor in the higher labor costs when planning your budget. On the other hand, systems that are easier to install, like liquid-applied membranes, may lower labor costs but might require more frequent reapplications or maintenance.
FAQs
Recent Blog Posts
Crawl Space News
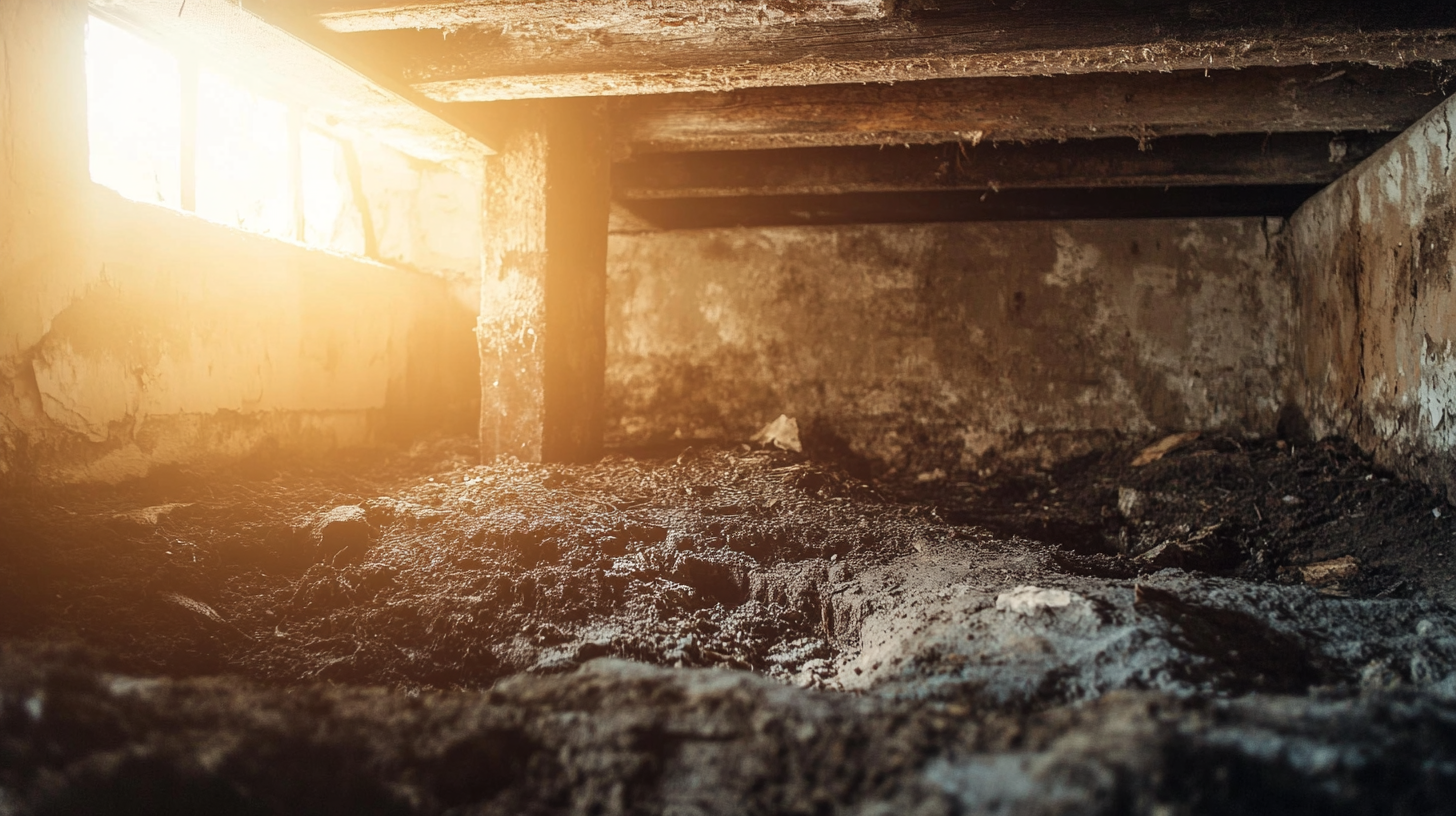
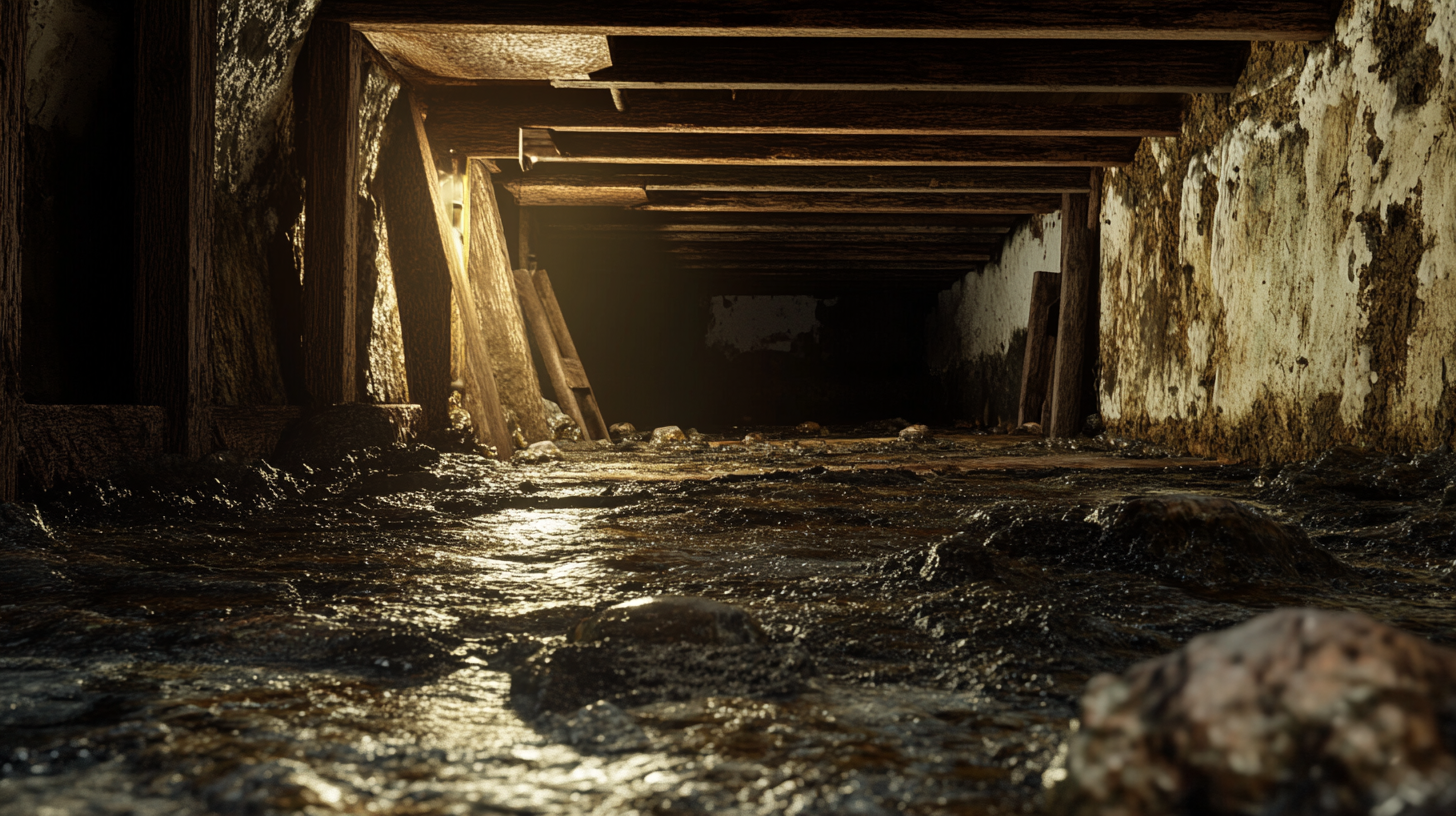
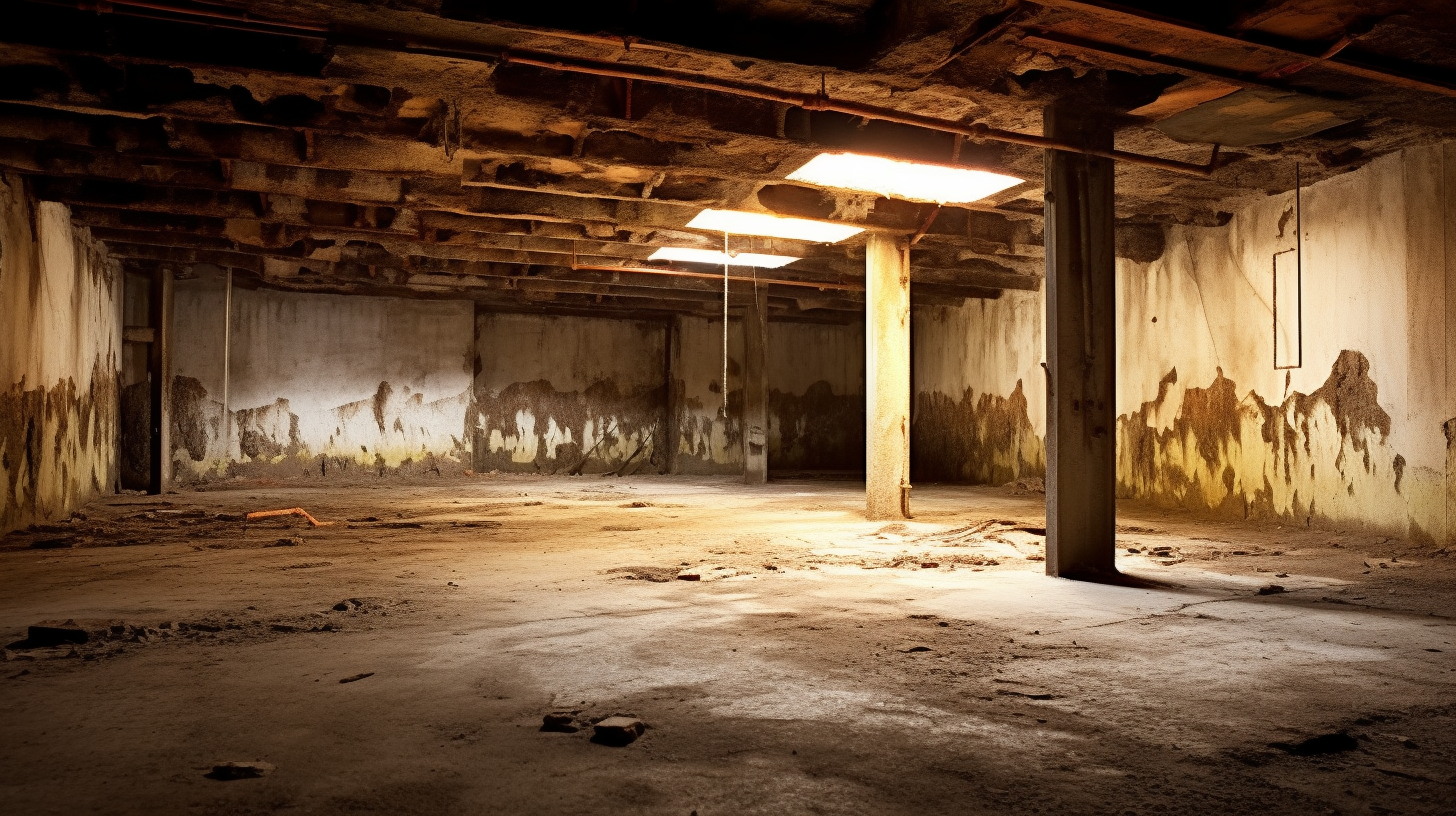