Now IS THe Time To...

Crawl Space Services In Knoxville, TN
Stetson Howard: 865-432-6743
CRAWL SPACE ENCAPSULATION, REPAIR, WATERPROOFING & MOLD REMOVAL
No-Obligation, Free Inspections
No-Obligation Free Estimates
We Warranty All of Our Work
100% Satisfaction Guaranteed
Waterproofing is an essential component in construction, ensuring that structures remain durable, safe, and functional over time. Whether it's residential buildings, commercial properties, or large-scale infrastructure, the importance of keeping water out cannot be overstated. Waterproofing safeguards buildings from moisture infiltration, which can lead to structural damage, mold growth, and a host of costly repairs. This practice not only protects the physical integrity of buildings but also contributes to the health and safety of occupants by preventing issues such as water damage, rot, and health risks associated with damp environments.
In the context of modern construction, waterproofing is recognized as a critical factor in sustainable building practices. By reducing the risk of water ingress, construction professionals can extend the lifespan of buildings, reduce maintenance costs, and improve energy efficiency. From below-ground waterproofing in foundations to above-ground solutions for roofs and facades, each system plays a vital role in a structure's overall durability. This comprehensive guide will explore the importance of waterproofing in construction, the various methods and materials used, and how it contributes to long-lasting, safe, and efficient building projects.
Understanding Waterproofing Systems
Waterproofing is a critical process in construction that protects structures from water penetration, ensuring long-term durability and safety. Whether it’s used in foundations, roofs, or walls, a proper waterproofing system prevents water damage, mold, and structural weakening. Effective waterproofing systems are designed to prevent water from entering areas where it could cause damage, thereby extending the life of a building and maintaining its integrity. In this section, we will explore what waterproofing entails and delve into the most common types of systems used in modern construction.
What is Waterproofing?
Definition and Explanation of Waterproofing in Construction
Waterproofing in construction refers to the process of making a structure water-resistant, so that it remains impervious to moisture and liquid water. This protection is essential in areas such as basements, roofs, and foundations, where prolonged exposure to water can lead to deterioration. In essence, waterproofing acts as a barrier that prevents water from passing through and damaging materials, protecting both the structural elements and interior spaces from moisture-related issues such as decay, corrosion, and mold growth.
Common Types of Waterproofing Systems
Waterproofing systems vary depending on the specific needs of a project and the environment it will be exposed to. Some of the most widely used waterproofing methods include:
- Liquid Membranes: These are applied in a liquid state and cure to form a seamless, flexible membrane. Liquid membranes can conform to a variety of shapes and surfaces, providing excellent coverage and protection. They are commonly used in roofing and foundation applications.
- Sheet Membranes: Pre-fabricated sheets of waterproofing material are applied to the surface, typically in overlapping layers to ensure full coverage. These sheets are made from materials such as rubber or modified bitumen, offering a durable and reliable barrier against water.
- Cementitious Waterproofing: This type of waterproofing uses a cement-based product mixed with specific bonding agents and is often applied to areas like water tanks, basements, and bridges. It is known for its strength and ability to form a solid, watertight layer.
Key Components of a Waterproofing System
An effective waterproofing system is composed of several essential elements, each contributing to the overall performance of the barrier. These components must work together seamlessly to ensure the structure remains watertight.
- Membranes: As the primary barrier, membranes are the most critical component of any waterproofing system. Whether applied in liquid or sheet form, the membrane must provide continuous coverage and resist water penetration. Membranes are typically flexible and durable to accommodate any movement or settling of the structure without cracking or compromising the seal.
- Sealants and Adhesives: Sealants and adhesives are used to ensure a strong, waterproof bond between materials, particularly at joints, edges, or around penetrations (such as pipes or vents). These products play a vital role in maintaining the integrity of the waterproofing system by sealing gaps that could allow water to enter.
- Substrate: The substrate is the surface onto which the waterproofing system is applied. The condition of the substrate can significantly affect the performance of the waterproofing system. It must be clean, smooth, and properly prepared to ensure the membrane adheres effectively and forms a continuous barrier.
- Drainage Systems: Effective drainage is essential to manage water flow around the structure, especially in areas prone to heavy rain or groundwater accumulation. Proper drainage prevents water from accumulating and applying pressure on the waterproofing system, reducing the risk of leaks and structural damage over time.
The Role of Material Compatibility in Waterproofing
Material compatibility plays a critical role in ensuring the effectiveness and durability of any waterproofing system. In construction, waterproofing systems are made up of various materials that must work together seamlessly to prevent water infiltration. However, if the materials used within the system are not compatible, they can lead to performance failures such as poor adhesion, degradation, or leakage. Understanding how different materials interact and ensuring their compatibility is essential for creating a reliable waterproofing barrier that stands the test of time. In this section, we will explore what material compatibility means and the factors that influence it in waterproofing systems.
What Does Compatibility Mean?
Definition of Material Compatibility in Waterproofing
In waterproofing, material compatibility refers to the ability of different components within the system to interact without causing degradation or failure. This includes ensuring that the membrane, substrate, sealants, and other elements work together effectively without reacting negatively. For example, the waterproofing membrane must adhere properly to the substrate, and sealants must bond effectively with both the membrane and surrounding surfaces. Material compatibility ensures that the system as a whole can withstand external pressures such as water, temperature fluctuations, and aging without compromising its protective function.
Interaction Between Different Materials Within a System
Every waterproofing system is composed of various materials that must interact harmoniously to create a continuous barrier against water. The membrane serves as the primary waterproof layer, but it relies on proper adhesion to the substrate, which must be prepared in such a way that it supports the membrane's application. Sealants are often used at joints or around penetrations to create watertight seals. The interaction between these materials is critical—if they are not compatible, it can result in poor performance, such as peeling, blistering, or cracking, which can ultimately lead to water ingress and damage.
Factors Influencing Compatibility
Several key factors can influence the compatibility of materials in a waterproofing system. These include the chemical makeup of the materials, their physical properties under stress, and how they age over time.
Chemical Composition
The chemical composition of materials used in waterproofing systems must be compatible to prevent negative reactions. Certain adhesives, for example, may react poorly with specific membranes, such as PVC (polyvinyl chloride) membranes, leading to degradation or loss of adhesion. Ensuring that all materials in the system are chemically compatible is crucial for maintaining the waterproofing barrier over time. Incompatible materials can cause rapid deterioration, leaving the system vulnerable to leaks and structural damage.
Thermal Expansion and Contraction
Waterproofing materials must be able to accommodate thermal expansion and contraction as temperatures fluctuate. Materials expand in the heat and contract in the cold, and if different components of the system respond to temperature changes at different rates, this can lead to cracks, gaps, or separations. For example, a membrane that expands significantly more than the underlying substrate can cause strain at the point of adhesion, potentially leading to failure over time. Ensuring that materials are chosen with similar expansion and contraction properties will help maintain the integrity of the system.
Adhesion Properties
The ability of a waterproofing material to adhere properly to the substrate and other system components is critical for creating a continuous, effective barrier. Proper adhesion ensures that the membrane and sealants remain firmly bonded to the substrate and surrounding materials, even under stress. Compatibility between the adhesive or bonding agents used and the waterproofing materials must be carefully considered. Poor adhesion can result in delamination or peeling, which compromises the system’s ability to prevent water infiltration.
Aging and Weathering
As waterproofing systems are exposed to the elements, aging and weathering naturally occur. Materials may degrade at different rates depending on their composition and environmental exposure. For instance, certain membranes may degrade more slowly than sealants, leading to cracks and gaps in the system if not properly accounted for. It is important to select materials that age and weather similarly to ensure the longevity of the waterproofing system. Compatibility in how materials withstand UV exposure, moisture, and temperature fluctuations is vital to maintaining performance over the long term.
Risks of Incompatibility in Waterproofing Materials
Waterproofing systems rely on the harmonious interaction of various materials to create a durable and effective barrier against water infiltration. However, when these materials are incompatible, the entire system is at risk of failure. Material incompatibility can lead to severe issues such as poor adhesion, cracking, and premature degradation, all of which compromise the waterproofing system's integrity. Understanding the risks associated with using incompatible materials is crucial for preventing costly repairs, structural damage, and potential safety hazards. This section will explore the common problems that arise from material incompatibility in waterproofing systems and provide real-world examples of both failures and successes.
Common Issues Arising from Material Incompatibility
Adhesion Failure
One of the most common problems caused by material incompatibility is adhesion failure. This occurs when the bonding between different components—such as the membrane, substrate, and sealants—is inadequate or breaks down over time. When materials do not adhere properly, gaps and openings can form, allowing water to penetrate the system. Adhesion failure is often due to incompatible adhesives or sealants being used with certain types of membranes, such as PVC or rubber, leading to water leaks and potential structural damage.
Cracking or Shrinkage
Materials in a waterproofing system must respond similarly to environmental changes, especially temperature fluctuations. When incompatible materials are used, they may expand or contract at different rates, leading to cracks, gaps, or shrinkage. For example, a membrane may expand significantly in heat, while the substrate or sealant does not. These stresses can cause the membrane to crack or pull away from the substrate, allowing water to seep in and compromise the system's effectiveness. Over time, this can lead to significant structural deterioration and expensive repairs.
Chemical Degradation
Chemical incompatibility between waterproofing materials can result in accelerated deterioration. When two materials react negatively with each other, their protective properties can degrade more quickly, reducing the system's lifespan. For instance, certain adhesives may react with specific types of membranes, causing them to break down or lose flexibility, leading to premature failure. This is particularly problematic in systems exposed to harsh environmental conditions, where chemical reactions can further exacerbate wear and tear.
Premature Failure
Using incompatible materials often leads to the premature failure of the entire waterproofing system. Even if only one component fails, it can affect the integrity of the whole system, significantly shortening its lifespan. Premature failure not only results in costly repairs and replacements but can also lead to extensive water damage, mold growth, and compromised structural safety. Proper material selection and ensuring compatibility between all components is crucial for the long-term success of a waterproofing system.
Real-World Examples of Incompatibility
Case Studies of Structural Water Damage Due to Material Incompatibility
One notable example of material incompatibility leading to failure occurred in a commercial building where an EPDM membrane was used alongside a bituminous-based adhesive. These two materials were chemically incompatible, leading to the breakdown of the adhesive bond over time. As a result, water began to seep into the building's foundation, causing significant water damage and requiring costly repairs. This case underscores the importance of selecting materials that are chemically compatible and can bond effectively over the long term.
Another case involved the use of a polyurethane sealant with a cementitious waterproofing system. Over time, the differing expansion and contraction rates of the sealant and the cement led to cracks in the system, allowing water to penetrate the structure. This issue could have been avoided by selecting a sealant that had similar expansion properties to the cementitious material.
Examples of Compatibility Success in Waterproofing Systems
On the other hand, there are numerous examples of successful waterproofing systems where careful attention to material compatibility resulted in long-lasting protection. In one case, a TPO (Thermoplastic Polyolefin) membrane was used in combination with a polymer-modified bitumen substrate, both of which had similar thermal expansion rates and excellent adhesion properties. This compatibility ensured that the system remained intact despite extreme weather conditions, preventing water infiltration for decades.
Another successful example involved the use of silicone-based sealants with EPDM membranes in a roofing system. Both materials exhibited high UV resistance and flexibility, allowing the system to withstand temperature fluctuations and environmental stress without cracking or degrading. This compatibility allowed the waterproofing system to function effectively for its full expected lifespan.
How to Ensure Compatibility in Waterproofing Material Choices
Ensuring the compatibility of waterproofing materials is essential for building a durable and effective system that protects against water infiltration. The right material combinations can prevent premature failure, while poor choices can lead to costly repairs and structural damage. Achieving material compatibility requires careful research, testing, and adherence to best practices. This section explores how to properly assess and ensure that the materials chosen for a waterproofing system will work harmoniously over the long term.
Conducting Proper Material Research
Importance of Understanding the Properties of Each Waterproofing Material
To ensure compatibility, it is critical to understand the properties of each material used in the waterproofing system. Different materials have unique chemical compositions, thermal expansion rates, and adhesion properties, all of which influence how they will interact when combined. For instance, certain adhesives work well with PVC membranes but may cause degradation if applied to EPDM membranes. Thorough research into the physical and chemical characteristics of each material helps avoid negative reactions and ensures the system performs as expected.
Reading Manufacturer Specifications and Compatibility Charts
A key part of material research is consulting the manufacturer specifications for each product. Manufacturers often provide detailed information on how their materials should be used, including compatibility charts that list which products can safely be combined. These specifications serve as a vital resource, outlining best practices and helping professionals avoid potentially harmful combinations. By following these guidelines, you can ensure that the materials will bond correctly and maintain their integrity over time.
Consulting Experts for Specialized Projects
In some cases, especially for specialized projects such as basements or roofs, it is beneficial to consult with waterproofing experts. Experts can offer valuable insights on which materials will work best in specific applications, taking into account factors like moisture levels, pressure from groundwater, or exposure to UV light. Their advice can be crucial in choosing the right materials that will perform well under the specific conditions of your project, helping to prevent costly failures down the line.
Testing for Compatibility
Pre-installation Tests: Conducting Adhesion and Compatibility Tests
Before fully installing any waterproofing system, it is advisable to conduct adhesion and compatibility tests. These pre-installation tests allow professionals to evaluate whether the chosen materials will bond effectively and remain durable over time. By testing small sections, you can observe how the materials interact and catch any potential issues before applying them on a larger scale. This step is especially important when working with materials that are not commonly paired together.
Sample Testing: Simulating Real Environmental Conditions
In addition to adhesion tests, conducting sample testing under conditions that mimic the real environment is essential. Exposing the materials to factors like heat, moisture, and UV light can reveal how they will respond once installed. For example, testing in a humid environment can show whether the materials will hold up against moisture or begin to degrade. These tests provide valuable data on how well the system will perform in actual field conditions, ensuring long-term compatibility.
Best Practices in Choosing Waterproofing Materials
Follow Manufacturer Guidelines
One of the most reliable ways to ensure compatibility is to follow the manufacturer guidelines for each material. Manufacturers typically provide clear instructions on how their products should be applied, including which other materials they are compatible with. By adhering strictly to these recommendations, you reduce the risk of using incompatible materials that could lead to failure or degradation of the waterproofing system.
Use Proven Systems
Where possible, it is advisable to use proven waterproofing systems—combinations of materials that have been tested and verified to work well together. Proven systems often come with guarantees or warranties, offering added peace of mind that the materials will perform as intended. By choosing materials with a track record of success in similar projects, you can minimize the risk of compatibility issues and ensure the longevity of the waterproofing system.
Consider Environmental Factors
The environmental conditions where the waterproofing system will be installed play a significant role in material compatibility. Factors such as UV exposure, temperature fluctuations, and moisture levels can all impact how materials interact over time. For instance, materials that are not UV-resistant may degrade quickly in sunny environments, while those with poor moisture resistance may fail in areas with high humidity. It is essential to select materials that are suited to the local climate and environmental conditions to ensure the system’s durability and effectiveness.
The Future of Compatibility in Waterproofing Systems
As the construction industry evolves, so does the technology behind waterproofing systems. Ensuring compatibility between waterproofing materials has always been critical, but the future promises innovations that will make this process even more efficient, reliable, and sustainable. With the development of advanced materials and a growing focus on eco-friendly solutions, waterproofing systems are poised to become more durable and environmentally conscious. This section explores the future of compatibility in waterproofing through innovations in material technology and sustainable practices.
Innovations in Waterproofing Materials
Advanced Chemical Formulations
One of the most exciting developments in waterproofing is the creation of advanced chemical formulations that enhance compatibility between materials. Manufacturers are developing new waterproofing membranes, adhesives, and sealants with improved bonding capabilities and greater resistance to environmental stressors like UV exposure and temperature fluctuations. These advanced materials are designed to work harmoniously, reducing the risk of chemical incompatibility and adhesion failure. For instance, next-generation adhesives are being engineered to form stronger bonds with a wider range of substrates, improving the overall durability and reliability of waterproofing systems.
These advancements in chemical engineering not only improve compatibility but also increase the performance of waterproofing systems in challenging environments. By reducing the need for constant maintenance and repairs, these innovations contribute to longer-lasting, more resilient buildings.
Hybrid Waterproofing Systems
The future of waterproofing also includes the rise of hybrid waterproofing systems, which combine materials with complementary properties to maximize performance. These systems integrate the strengths of different materials—such as the flexibility of liquid membranes and the durability of sheet membranes—to create a more versatile and robust waterproofing solution. Hybrid systems can offer enhanced resistance to water penetration, improved thermal expansion properties, and greater adaptability to varying environmental conditions.
For example, combining polyurethane coatings with bitumen membranes can provide superior waterproofing for both above-ground and below-ground structures, with the polyurethane offering flexibility and the bitumen providing strength and longevity. These hybrid approaches enable the creation of waterproofing systems that are more adaptable to complex construction projects, ensuring better material compatibility and longer-term performance.
Sustainability and Eco-Friendly Waterproofing
Choosing Compatible Materials that are Environmentally Friendly
As sustainability becomes a key focus in construction, the need for environmentally friendly waterproofing materials is growing. Future waterproofing systems will not only need to be compatible with one another but also with the environment. This means selecting materials that have a lower environmental impact—such as those made from recycled materials or bio-based compounds—and ensuring that these materials can work together seamlessly. For instance, eco-friendly membranes made from renewable resources are being developed to be fully compatible with non-toxic adhesives and sealants, reducing the use of harmful chemicals and minimizing the environmental footprint of waterproofing systems.
The Role of Compatibility in Reducing Waste and Extending Lifespan
Ensuring the compatibility of waterproofing materials also plays a significant role in reducing waste and extending the lifespan of waterproofing systems. When materials fail due to incompatibility, it often results in the premature removal and replacement of entire systems, generating unnecessary waste and consuming additional resources. By selecting materials that are specifically designed to work together, construction professionals can create waterproofing systems that last longer and require fewer replacements or repairs, leading to more sustainable building practices.
Additionally, compatible systems are easier to maintain, reducing the need for frequent interventions and lowering the overall environmental impact. As the industry continues to innovate, the integration of sustainable materials with enhanced compatibility will be key to creating waterproofing solutions that not only protect structures but also support environmental goals.
FAQs
Recent Blog Posts
Crawl Space News
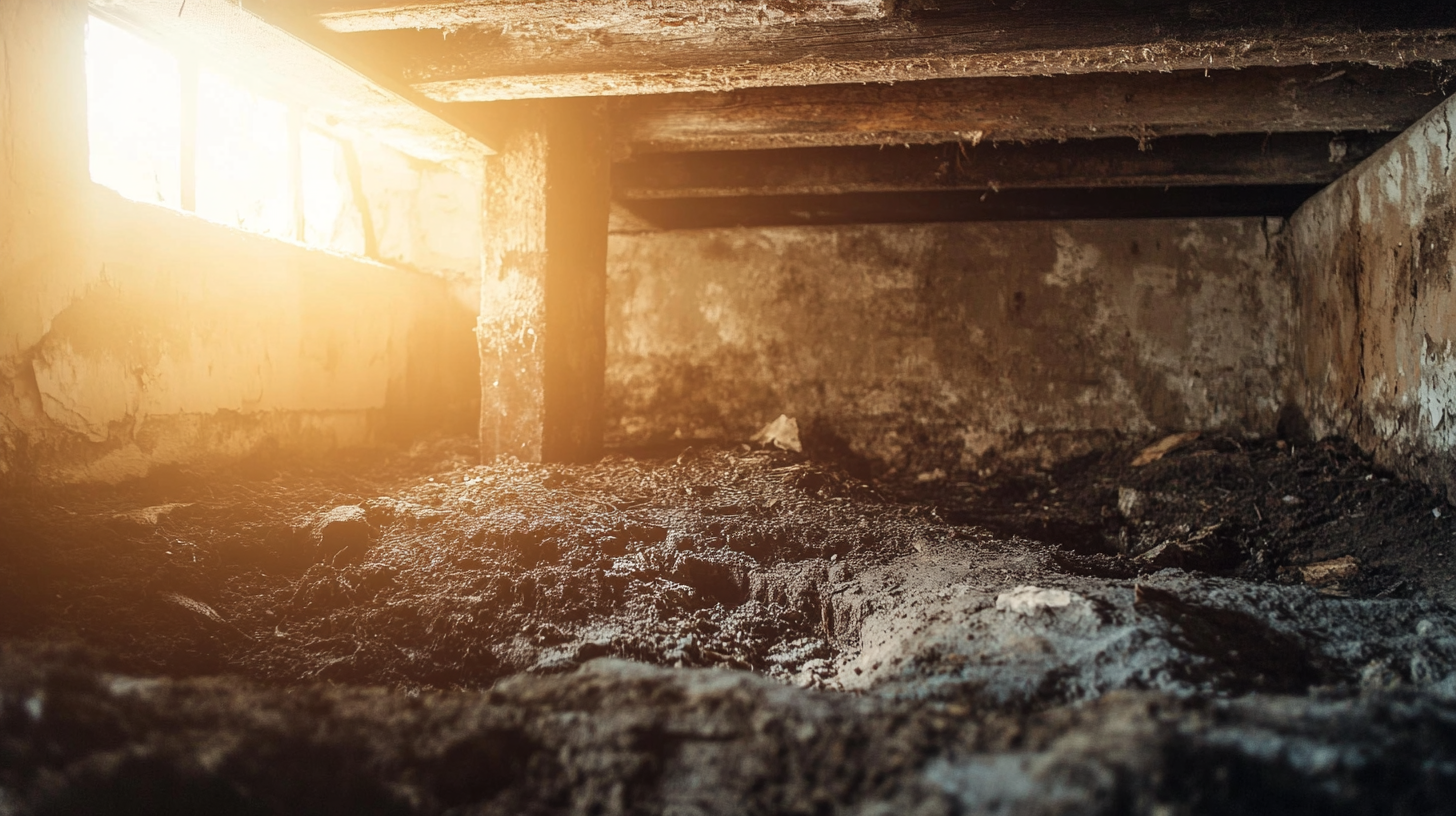
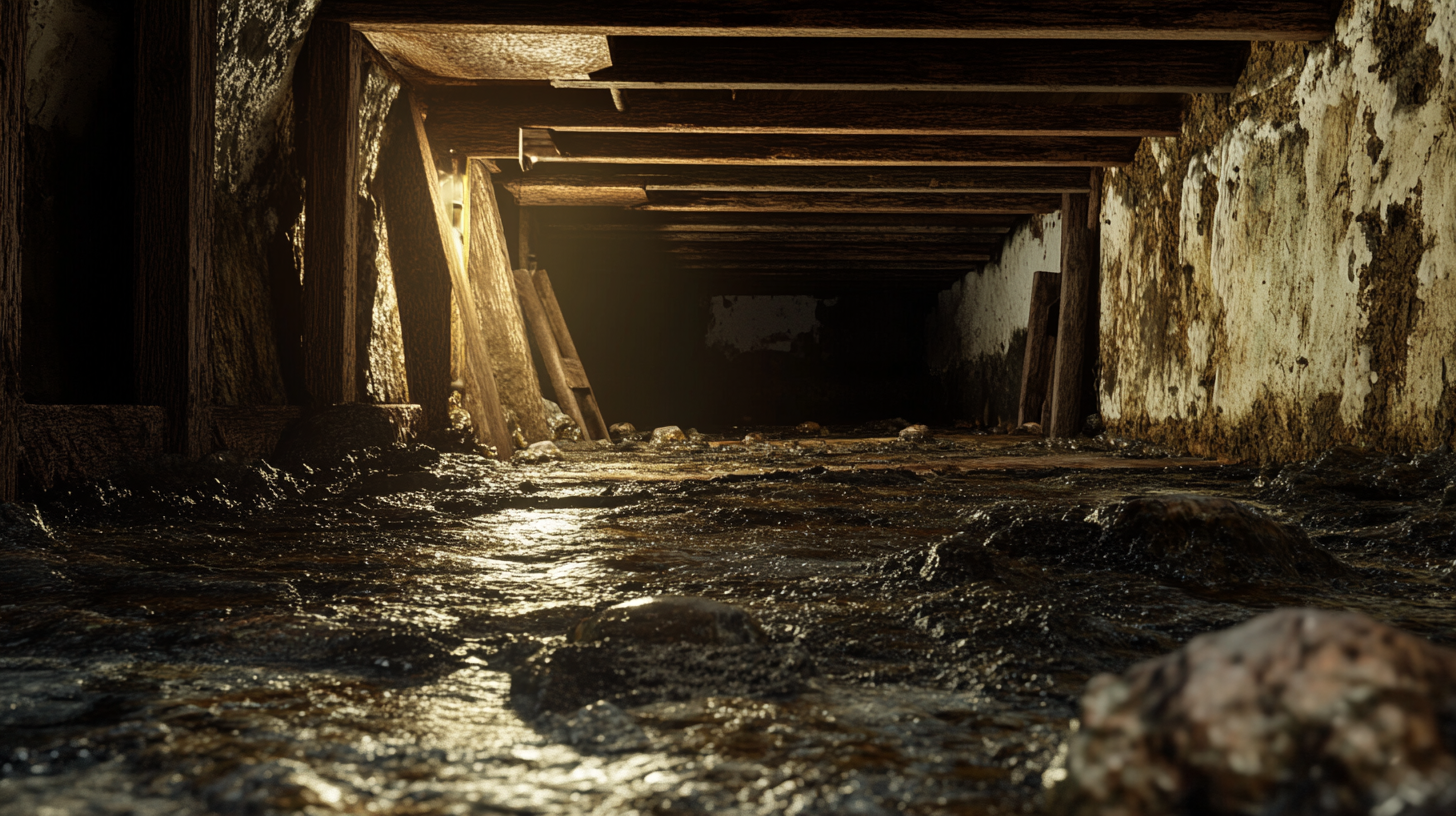
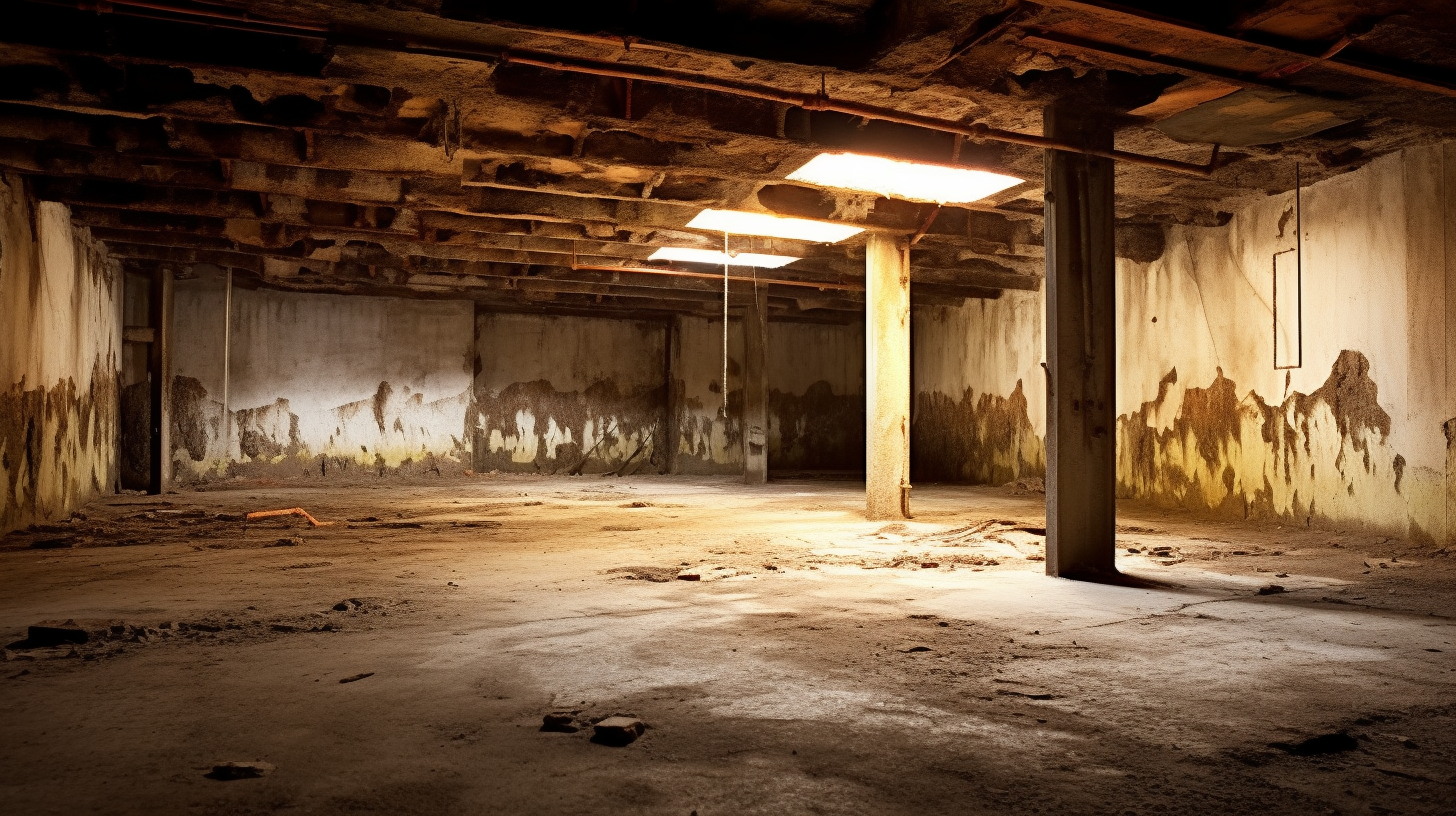