Now IS THe Time To...

Crawl Space Services In Knoxville, TN
Stetson Howard: 865-432-6743
CRAWL SPACE ENCAPSULATION, REPAIR, WATERPROOFING & MOLD REMOVAL
No-Obligation, Free Inspections
No-Obligation Free Estimates
We Warranty All of Our Work
100% Satisfaction Guaranteed
Welcome to our insightful exploration into the world of concrete structures and the pivotal role of waterproofing in preserving their integrity and longevity. In this blog, we delve into why waterproofing is not just an optional enhancement but an essential component in the construction and maintenance of concrete buildings and infrastructures.
Understanding the Importance of Waterproofing Concrete
Concrete, known for its strength and durability, is a fundamental material in modern construction. However, its porous nature makes it susceptible to water penetration, leading to deterioration over time. Waterproofing is therefore crucial in protecting concrete structures from the damaging effects of moisture, such as corrosion, freeze-thaw cycles, and chemical attacks. This protection is vital in extending the lifespan of structures and ensuring their safety and functionality.
The Unique Challenges of Waterproofing Concrete
Waterproofing concrete presents unique challenges due to its specific characteristics:
Porosity of Concrete: The inherent porosity of concrete means that water can seep in, necessitating a robust waterproofing strategy.
Chemical Reactions: Concrete can undergo chemical reactions when exposed to water, leading to weakening and degradation.
Structural Movement: Concrete structures can expand and contract with temperature changes, requiring waterproofing solutions that accommodate this movement.
Environmental Factors: Exposure to varying weather conditions and environmental pollutants can also impact the effectiveness of waterproofing measures.
In this blog, we will explore these challenges in detail, providing insights into the best practices for waterproofing concrete structures. From the selection of appropriate waterproofing materials to the application techniques and maintenance considerations, we aim to equip you with the knowledge to effectively safeguard your concrete structures against water-related damages.
Join us as we navigate the complexities of concrete waterproofing, highlighting its importance and the unique considerations it entails, to ensure the resilience and durability of your structures.
Understanding Concrete and Its Vulnerabilities
Concrete is a fundamental material in construction, known for its strength and versatility. However, it has inherent vulnerabilities that need to be addressed to maintain the integrity of structures built with it. This section explores the properties of concrete, how they affect its waterproofing needs, and the common issues that arise in concrete structures.
Properties of Concrete
Composition and Characteristics of Concrete
Concrete is a composite material made from a mixture of cement, water, aggregates (like sand and gravel), and sometimes additives. Its key characteristics include:
- Strength: Concrete is known for its considerable compressive strength.
- Durability: It can withstand a variety of environmental conditions.
- Thermal Mass: Concrete has a high thermal mass, meaning it can absorb and retain heat.
- How These Properties Affect Its Waterproofing Needs
Despite its strengths, concrete's properties also create specific waterproofing challenges:
- Porosity: Concrete is porous, allowing water and moisture to penetrate through microscopic pores and capillaries.
- Cracking: It can develop cracks over time due to shrinkage, temperature changes, or structural stress.
- Chemical Reactions: Concrete can undergo chemical reactions when exposed to water, leading to weakening and degradation.
Common Issues with Concrete Structures
Identifying Typical Problems Like Cracks, Porosity, and Water Seepage
Common issues in concrete structures include:
- Cracks: These can range from hairline surface cracks to deeper structural cracks.
- Porosity: The porous nature of concrete makes it susceptible to water ingress.
- Water Seepage: This can occur in areas like basements, foundations, and walls, especially in the presence of groundwater or heavy rainfall.
- Long-Term Effects of Water Damage on Concrete
Water damage in concrete structures can lead to:
- Structural Deterioration: Prolonged water exposure can weaken the structural integrity of concrete.
- Corrosion of Reinforcements: Water seepage can cause the corrosion of steel reinforcements, further compromising structural strength.
- Mold and Mildew Growth: Moisture accumulation can lead to mold and mildew, posing health risks and degrading the quality of indoor environments.
- Freeze-Thaw Damage: In colder climates, water absorbed in concrete can freeze and expand, leading to further cracking and damage.
Waterproofing Methods for Concrete
Waterproofing concrete is essential to protect it from water-induced damage. Various methods can be employed, each with its own set of advantages and application techniques. This section will cover surface coatings and sealants, membrane waterproofing, and integral waterproofing, providing insights into their effectiveness and suitability for different concrete structures.
Surface Coatings and Sealants
Types of Coatings and Sealants Suitable for Concrete
Several types of coatings and sealants are effective for waterproofing concrete:
- Acrylic Coatings: These are water-based and ideal for surfaces that need a breathable waterproof layer.
- Epoxy Coatings: Known for their durability, they are suitable for floors and areas with heavy usage.
- Polyurethane Sealants: Flexible and strong, these are used for sealing joints and cracks in concrete.
- Application Techniques for Effective Coverage
Proper application is key to the effectiveness of coatings and sealants:
- Surface Preparation: Ensure the concrete surface is clean, dry, and free of any debris or previous coatings.
- Application Tools: Use brushes, rollers, or sprayers depending on the type of coating or sealant.
- Even Application: Apply in a uniform layer, following the manufacturer's instructions for thickness and number of coats.
- Curing Time: Allow adequate time for the coating or sealant to dry and cure completely.
Membrane Waterproofing
Explanation of Membrane Waterproofing Systems
Membrane waterproofing involves applying a thin layer of water-resistant material over the concrete surface. There are two main types:
- Sheet-Based Membranes: These are pre-fabricated sheets of waterproof material, adhered to the concrete surface.
- Liquid-Applied Membranes: Applied in liquid form and cure to form a seamless, flexible waterproof layer.
Pros and Cons of Different Membrane Types
- Sheet-Based Membranes: Pros include high durability and resistance to punctures. Cons can be the complexity of installation and the need for professional application.
- Liquid-Applied Membranes: Pros include ease of application and suitability for irregular shapes. Cons may include sensitivity to application conditions and potential for uneven coverage.
- H3: Integral Waterproofing
- How Integral Waterproofing Works Within the Concrete Mix
- Integral waterproofing involves adding waterproofing agents to the concrete mix before it is poured. These agents disperse throughout the concrete, filling pores and capillaries, and making the entire mass water-resistant.
Situations Where Integral Waterproofing is Most Effective
- New Construction: Ideal for new projects where waterproofing can be incorporated from the start.
- Areas with High Moisture Exposure: Effective in basements, foundations, and other areas prone to water exposure.
- Large Concrete Structures: Suitable for projects where applying external waterproofing is impractical.
Preparing Concrete for Waterproofing
Proper preparation of concrete surfaces is crucial for effective waterproofing. This preparation not only enhances the adherence and effectiveness of waterproofing materials but also extends the life of the concrete structure. This section will guide you through the essential steps for preparing concrete surfaces and techniques for repairing cracks, ensuring a solid foundation for any waterproofing application.
Surface Preparation
Steps for Preparing Concrete Surfaces Before Waterproofing
Effective waterproofing starts with thorough surface preparation:
- Cleaning the Surface: Remove dirt, debris, and any existing coatings. Pressure washing or scrubbing with a detergent can be effective.
- Removing Mold and Mildew: Treat any areas with mold or mildew with a suitable cleaner to prevent future growth.
- Leveling Uneven Areas: Use a concrete patching compound to fill in holes or level uneven surfaces.
- Allowing the Surface to Dry: Ensure the concrete is completely dry before applying waterproofing materials.
Importance of Addressing Existing Damage
Addressing existing damage is vital for several reasons:
- Ensuring Adhesion: Waterproofing materials adhere best to surfaces that are clean and intact.
- Preventing Future Issues: Unaddressed damage can lead to further deterioration, compromising the waterproofing.
Assessing and Repairing Cracks
Techniques for Repairing Cracks in Concrete Prior to Waterproofing
Before waterproofing, it's essential to repair any cracks:
- Identifying Crack Types: Determine if the cracks are structural or non-structural.
- Cleaning the Cracks: Remove loose material from the cracks using a wire brush or similar tool.
- Filling the Cracks: Use a concrete crack filler or sealant for non-structural cracks. Structural cracks may require more complex solutions like epoxy injections.
- Preventative Measures to Minimize Future Cracking
To minimize future cracking:
- Control Joints: Install control joints to manage the expansion and contraction of concrete.
- Proper Curing: Ensure concrete is cured properly to reduce the likelihood of cracking.
- Regular Maintenance: Conduct regular inspections and maintenance to address any issues promptly.
Application Techniques for Concrete Waterproofing
Effective waterproofing of concrete structures is key to ensuring their longevity and durability. This section provides a detailed guide on the best practices for applying coatings and sealants, as well as step-by-step instructions for installing waterproofing membranes, along with tips to overcome common challenges.
Best Practices for Applying Coatings
Detailed Guide on Applying Coatings and Sealants to Concrete
Applying coatings and sealants correctly is crucial for effective waterproofing:
- Choose the Right Product: Select a coating or sealant that is suitable for the concrete surface and the environmental conditions it will face.
- Prepare the Surface: Ensure the concrete surface is clean, dry, and free of any debris or previous coatings.
- Apply Primer if Needed: Some products may require a primer for better adhesion.
- Use the Correct Tools: Brushes, rollers, or sprayers are typically used, depending on the product and surface area.
- Apply Evenly: Follow the manufacturer's instructions for application, ensuring even coverage. Avoid thick layers that can lead to cracking or bubbling.
Tips for Achieving Uniform Coverage and Optimal Protection
- Work in Favorable Conditions: Avoid extreme temperatures or wet weather during application.
- Multiple Thin Layers: Apply multiple thin layers rather than one thick layer for better curing and durability.
- Curing Time: Allow adequate time for each layer to dry and cure properly before applying the next.
Installing Waterproofing Membranes
Step-by-Step Instructions for Membrane Installation
Waterproofing membranes require careful installation:
- Surface Preparation: Start with a clean, smooth, and dry concrete surface.
- Measure and Cut Membrane: Measure the area and cut the membrane to size, allowing for some overlap at seams.
- Apply Adhesive: If using a self-adhesive membrane, remove the backing and apply. For other types, apply the adhesive to the concrete surface as directed.
- Position the Membrane: Carefully lay the membrane onto the surface, smoothing out any wrinkles or bubbles.
- Seal the Seams: Ensure all seams are tightly sealed and overlapped according to manufacturer instructions.
Common Challenges and How to Overcome Them
- Air Bubbles: Use a roller to smooth out bubbles as you lay the membrane.
- Seam Sealing: Use a high-quality seam sealer and ensure thorough coverage for watertight seams.
- Corners and Edges: Pay extra attention to corners and edges, ensuring they are fully covered and sealed.
Maintenance and Care of Waterproofed Concrete
Proper maintenance and care are essential to ensure the longevity and effectiveness of waterproofed concrete structures. Regular checks and timely repairs can prevent minor issues from escalating into major problems. This section offers guidance on establishing a maintenance routine, identifying signs of wear or failure, and addressing common waterproofing issues.
Routine Maintenance Tips
Maintenance Schedule for Waterproofed Concrete Structures
A consistent maintenance schedule is key to preserving waterproofed concrete:
- Bi-annual Inspections: Conduct thorough inspections at least twice a year, preferably in spring and fall.
- After Severe Weather: Check for damage after extreme weather events, such as heavy rain or freezing temperatures.
- Identifying Signs of Wear or Failure
Be vigilant for signs that indicate waterproofing issues:
- Visual Inspection: Look for cracks, peeling, or blistering in the waterproof coating.
- Water Stains: Check for water stains or damp spots on the interior surfaces of the concrete structure.
- Mold and Mildew: The presence of mold or mildew can indicate moisture penetration.
- Efflorescence: White, powdery residue on the concrete surface can be a sign of water seepage.
Repairing Waterproofing Failures
How to Address and Repair Common Waterproofing Issues
Effective repair strategies depend on the type and extent of the damage:
- Cracks and Small Holes: Clean the area and fill with a suitable waterproof sealant or concrete patching compound.
- Peeling or Blistering Coatings: Remove the damaged coating, prepare the surface, and reapply a new layer of waterproofing material.
- Drainage Issues: Ensure that gutters, downspouts, and drainage systems are clear and functioning properly to prevent water accumulation.
- When to Seek Professional Assessment and Intervention
Some situations require professional expertise:
- Structural Cracks: Large or expanding cracks might indicate structural issues and need professional assessment.
- Recurrent Water Seepage: If water seepage persists despite repairs, it may be due to underlying issues that require expert diagnosis.
- Extensive Damage: For widespread damage or deterioration, professional repair services can ensure a comprehensive and lasting solution.
FAQs
Recent Blog Posts
Crawl Space News
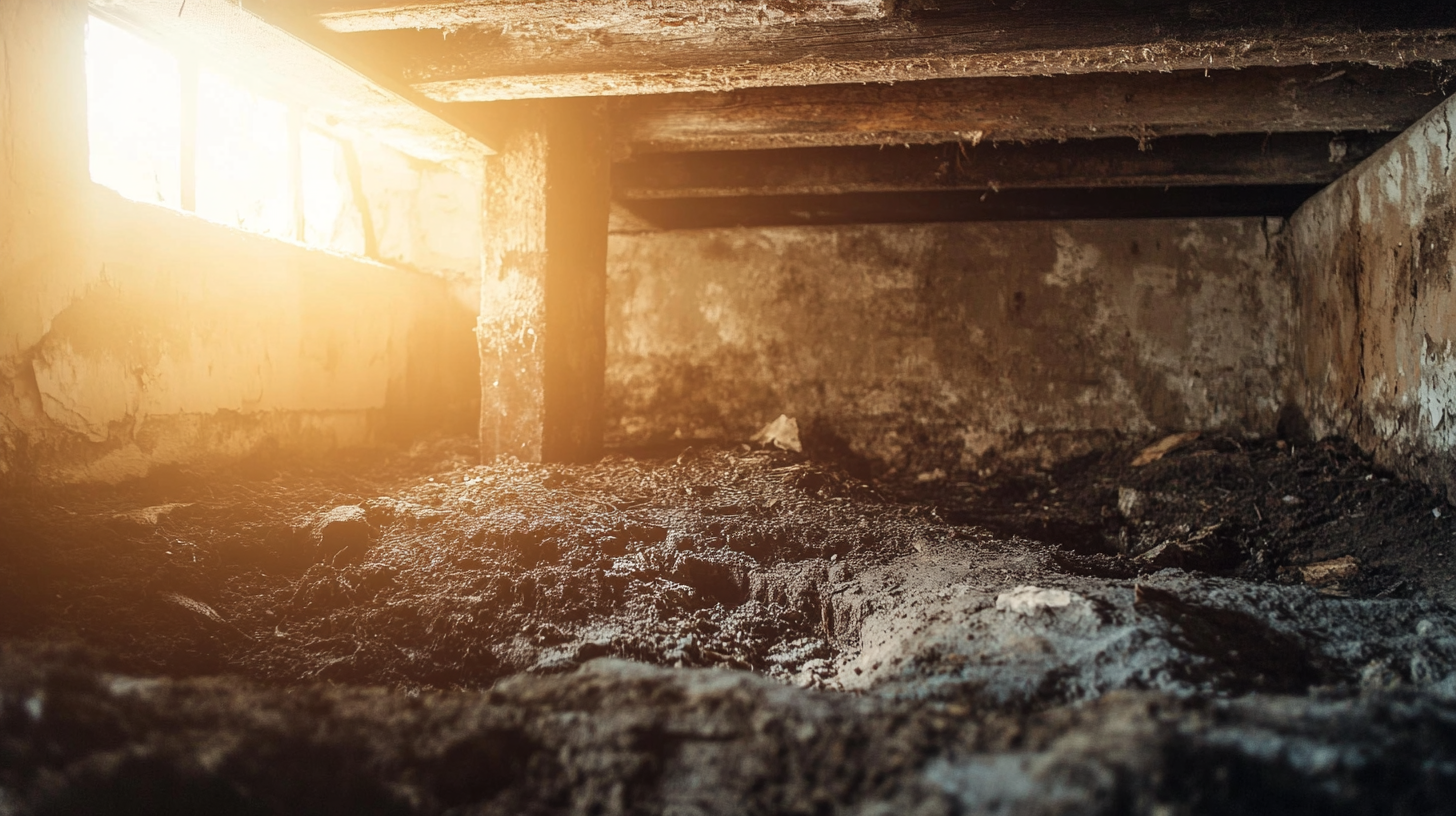
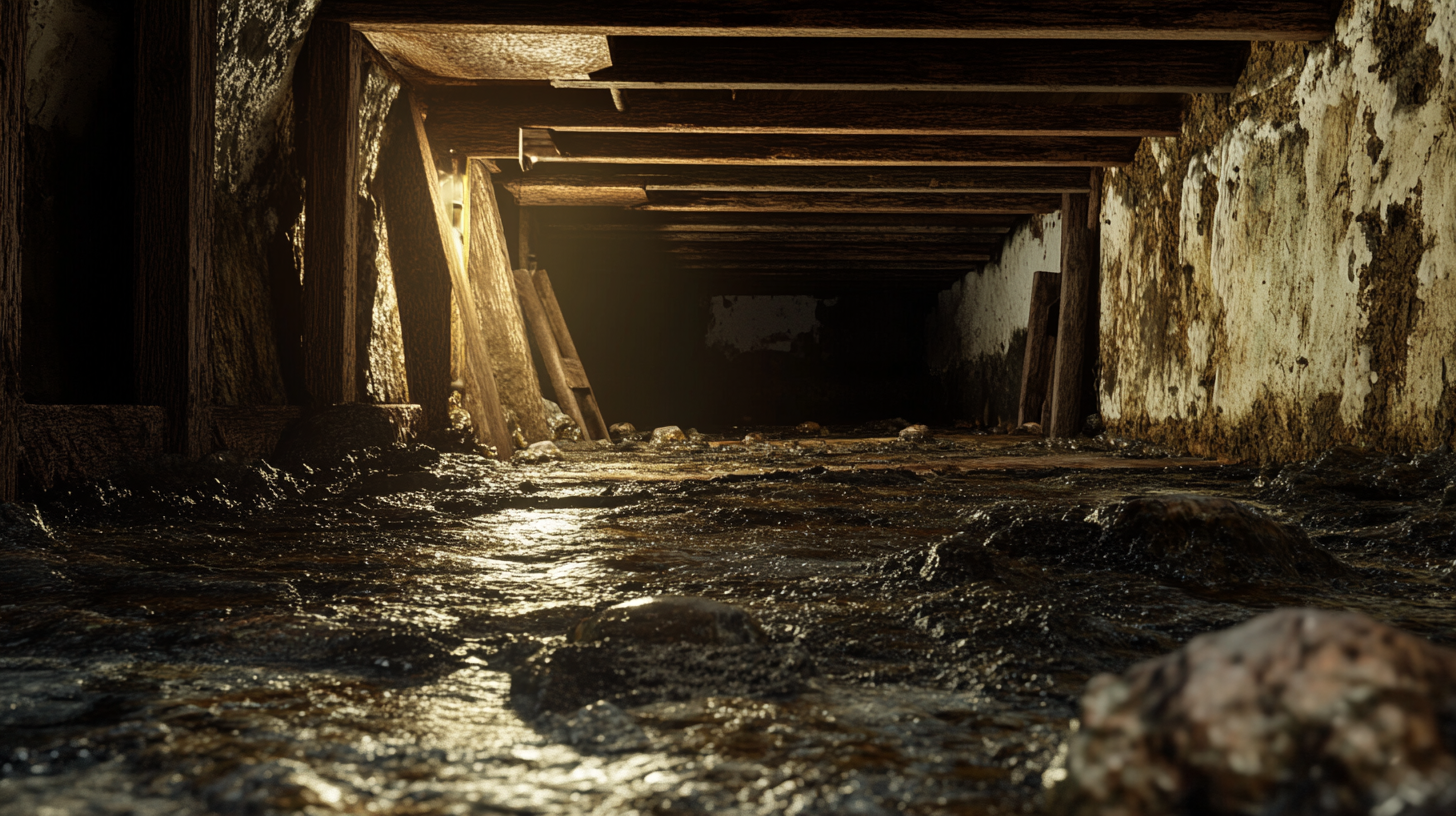
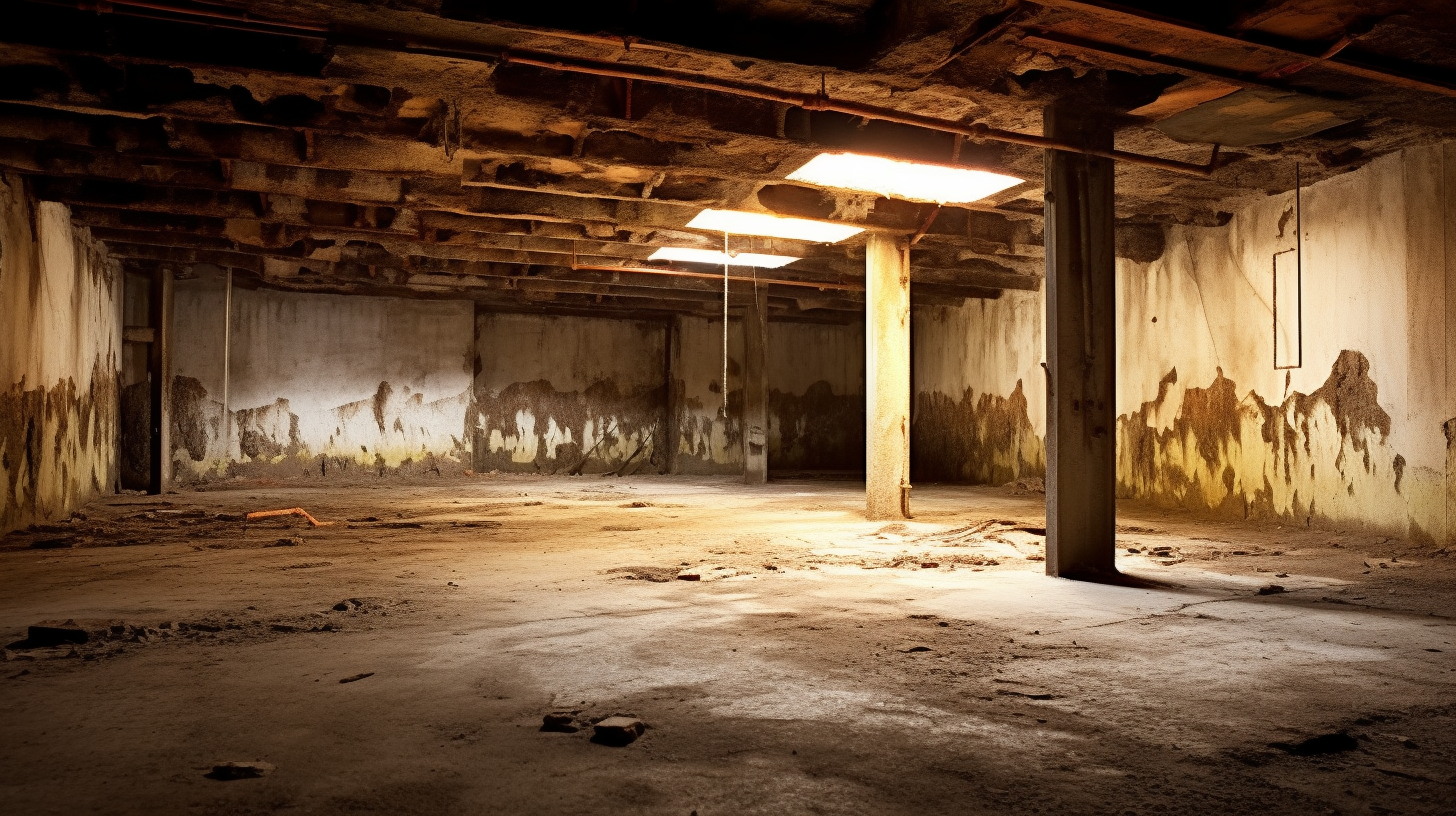